903.21 Construction Inspection Guidelines for Sec 903
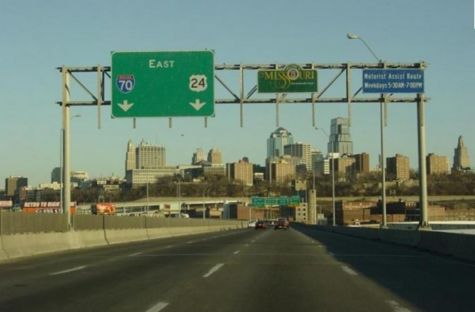
903.21.1 General (for Sec 903.1)
The contractor is responsible for erection of highway signing in accordance with the plans, specifications and provisions. The construction inspector should provide quality assurance oversight to ensure proper installation.
903.21.2 Staking, Layout and Hold Points
The contractor is responsible for all staking and layout. The Resident Engineer should include “Verification of highway signing locations” on the list of contractor Hold Points. After the contractor stakes the sign locations, the inspector should review each location with the contractor and determine whether there are any conflicts with other signs or roadway items and adjust as necessary. District Traffic personnel should be consulted before making any significant changes to the planned location. For large signing projects, it is recommended to invite district Traffic staff to the hold point evaluation of sign locations. Once grading of the slopes is complete, and the sign locations are approved by the engineer, the contractor will have the information needed to determine the post lengths. To save time, some contractors prefer to pre-order extra length for posts and field cut to the required length. No payment should be made for excess cut-offs.
903.21.3 Base Construction Inspection (for Sec 903.3)
Excavating, forming, pouring and curing of concrete sign bases will be done in accordance with contract requirements. Inspection of these operations is similar to procedures set out in Division 700 of the Missouri Standard Specifications for Highway Construction for structures. Galvanized signposts are not to be stored on the ground. Storage on the ground for lengthy periods results in stained and unsightly posts. Ensure the base, post and sign installation details are in accordance with the standard plans. The inspector should check welds on cover plates and base plates of bolt-down posts for rust spots. These and other small areas where galvanizing has been chipped off due to rough handling should be cleaned and repaired. If a post shows considerable rust along welds, it should be rejected. The area around washers and bolts on breakaway features is to be free of beads and runs so a true value is obtained for torque requirements.
903.21.4 Sign Inspection
The inspector is to make a careful inspection of signs when they arrive on the project site and that they are stored properly. Signs should be stored vertically and not in contact with the ground or vegetation. Moisture trapped between signs can damage the reflectivity. When signs are unpacked, carefully inspect each sign for damage incurred in packaging or in transit and for errors in copy. Make spot checks of letter and numeral height and spacing using the original plan drawings as a guide.
Night inspections as well as daytime inspections should be made of all signs, delineators and mileposts. Make night inspections to check reflectivity of signs and delineators. Sign erection inspection consists not only of checking sign faces during erection but also of making certain the panel has minimum plan horizontal and vertical clearances. The sign is to be erected so that its top edge is horizontal and its vertical edges plumb. Skew angle should be 93° from the roadway. Refer to Standard Drawings for details.
903.21.5 Truss Erection
Normally, plan truss locations are carefully checked before the project is placed under contract. There have been very few occasions when they have had to be moved to clear a roadway structure. However, if a truss’s location needs to be changed, district Traffic and district Design should be consulted. Features that should not be altered when moving a truss are:
- (1) Maintain the 17 ft. 6 in. minimum clearance from the highest point of pavement to the lowest member of the truss.
- (2) Check for possible conflicts with overhead power transmission lines. Refer to Sec 901.1.
Staking, excavating, forming and concreting of truss footings and pedestals are similar to operations performed when building a bridge footing. Inspection procedure should follow, in general, instructions set out in Division 700 of the Missouri Standard Specifications for Highway Construction. In addition, conduit run through the truss pedestal is to be properly capped to prevent concrete from entering during placement.
When truss erection is done after the roadway is opened to traffic, the inspector will make certain the contractor takes necessary measures to ensure traffic protection. If traffic will have to be stopped for truss erection, the inspector is to require the contractor to have all pre-erection column adjustments made in advance. The contractor should have all necessary workers and erection materials at hand before traffic is stopped so the least possible delay occurs. The inspector should instruct the contractor to adjust the columns for the overhead truss to the proper spacing by use of the leveling nuts. Proper spacing depends on the material from which the truss is fabricated and the temperature of the truss material at time of erection.
Plans for both aluminum and steel overhead trusses generally show one inch of collar space on each side of the column at a temperature of 55º F. A temperature correction should be made by adjustment of the base leveling nuts. For example, if a 75 ft. steel truss is to be erected at a metal temperature of 110º F, the following calculations are to be made:
- Using a coefficient of expansion for steel of 0.0000065 per degree Fahrenheit, the correction would be:
- (110º - 55º) x 75 x 0.0000065 = 0.027 ft. = 5/16 in.
Each space, nearest to the roadway, between the collar and the column should be reduced by 5/32 inch. If the same length truss is aluminum, the coefficient of expansion for aluminum is 0.000013 per degree Fahrenheit and the correction would be:
- (110º - 55º) x 75 x 0.000013 = 0.054 ft. = 5/8 in.
Each space, nearest the roadway, between column and collar should then be reduced by 5/16 inch. Conversely, if metal temperature is below 55º F, column tops should be adjusted to increase the space by the amount calculated. The foregoing calculations were made on the assumption that the truss columns were spaced plan distance apart and that the truss was fabricated to plan length. Any variation from plan in either case will have to be taken into consideration and adjustments made accordingly.
The foregoing instructions are given with the knowledge that most overhead trusses, over a period of time, gradually shift left or right and finally bear against the collar. This is probably due to traffic vibration and to unequal coefficients of friction between column and truss bearing areas. However, it is essential to set the truss on the columns with proper spacing, based on temperature, between each column and its respective collar during initial erection.