Job Special Provisions and Category:109 Measurement and Payment: Difference between pages
No edit summary |
→109.1 Measurement of Quantities (for Sec 109.1): updated per RR3958 |
||
Line 1: | Line 1: | ||
[[Image:237.3 Quantities.jpg|right|325px]] | |||
This article provides additional guidance related to measurement and payment, as defined in [http://www.modot.org/business/standards_and_specs/SpecbookEPG.pdf#page=4 Sec 109], and sets forth uniform and effective procedures for the maintenance of records necessary to document project payments. Documentation procedures shown are considered to be the minimum required to authorize payment for an item. It is not intended to discourage other or more detailed documentation should either or these be appropriate to the situation. | |||
It is intended that detailed records be prepared for all items and especially for those not accessible when a project is complete or for any pay item that does not remain a part of a completed project. | |||
The specifications provide the basis of payment and a description of most items. Field measurement, final plans and remarks instructions are included in this article for that specification or may be obtained from the [http://sp/sites/cm/Pages/default.aspx Constructions and Materials division]. | |||
{|style="padding: 0.3em; margin-left:2px; border:2px solid #a9a9a9; text-align:center; font-size: 95%; background:#f5f5f5" width="325px" align="right" | |||
|- | |||
|EPG articles are <u>not</u> referenced as "sections" but as EPG XXX.X to avoid confusion with MoDOT specs (which are contractually binding). | |||
| | |||
| | |||
| | |||
|} | |} | ||
==109.1 Measurement of Quantities (for [http://www.modot.org/business/standards_and_specs/SpecbookEPG.pdf#page=4 Sec 109.1])== | |||
{|style="padding: 0.3em; margin-left:7px; border:2px solid #a9a9a9; text-align:center; font-size: 95%; background:#f5f5f5" width="275px" align="right" | |||
|- | |||
|<center>'''Forms'''</center> | |||
|- | |||
|[https://epg.modot.org/forms/CM/Force_Account_Spreadsheet.xlsx Force Account Spreadsheet] | |||
|- | |||
|[[media:137 Force Account Worksheet example.xls|Force Account Worksheet example]] | |||
|- | |||
|<center>'''Quick Reference Guides to assist in the AWP change order process:'''</center> | |||
|- | |||
|[https://epg.modot.org/forms/CM/AWP_CO_Change_Order_Reports.doc Change Order Reports] | |||
|- | |||
|[https://epg.modot.org/forms/CM/AWP_CO_1ChangeOrderOverview.doc Change Order Overview] | |||
|- | |||
|[https://epg.modot.org/forms/CM/AWP_CO_Change_Order_Codes.docChange Order Codes] | |||
|- | |||
|[https://epg.modot.org/forms/CM/AWP_CO_3ChangeOrderTimeExtension.doc Change Order Time Extension] | |||
|- | |||
|[https://epg.modot.org/forms/CM/AWP_CO_4ChangeOrderValueEngineering.doc Change Order Value Engineering] | |||
|- | |||
|[https://epg.modot.org/forms/CM/AWP_CO_5ChangeOrderNoCostContractModification.doc Change Order, No Cost Contract Modification] | |||
|- | |||
|[https://epg.modot.org/forms/CM/AWP_CO_Milestones.docMilestones] | |||
|- | |||
|<center>'''Quick Reference Guide to assist in the AWP payment estimate process:'''</center> | |||
|- | |||
|[https://epg.modot.org/forms/CM/AWP_CO_Contract_Adjustments.doc Contract Adjustments] | |||
|- | |||
|[https://epg.modot.org/forms/CM/AWP_CO_Estimate.doc Contractor Pay Estimates] | |||
|- | |||
|[https://epg.modot.org/forms/CM/AWP_CO_Item_Adjustments.doc Line Item Adjustments] | |||
|- | |||
|[https://epg.modot.org/forms/CM/AWP_CO_Construction_Stockpiles.doc Stockpiled Materials] | |||
|} | |||
Measurements performed, and the associated calculations, should be well documented in the project records and should be recorded to no less than the minimum specified precision of the measurement. (For example: “Measurement will be made to the nearest linear foot” means to measure to no less than the nearest linear foot.) Confirm that the tools being used to make the measurement are accurate within the range required for the measurement. Calculations may be made manually, with a calculator or a computer but in each instance the results should be independently verified to eliminate math, keystroke or computer related errors. | |||
Specifications typically have a "Method of Measurement" clause that indicates the minimum unit of measurement and pay. Each day that a work item is reported, the total quantity of work completed or material placed that day is to be totaled and then reported to a degree of accuracy no less than what is designated in the specification. Rounding is generally not necessary. For instance, tickets for hot mix asphalt generally show the measured quantity to the nearest hundredth of a ton even though the degree of accuracy per spec is only required to be to the nearest tenth of a ton. The tickets should be totaled to the nearest hundredth and reported to that accuracy in AWP each day. The daily quantity does not need to be rounded nor does the final pay quantity at project closeout need to be rounded. | |||
When payment is made per station, it should be assumed that the work is performed in a single pass through the project limits and that the work may be along the centerline, on either side or on both sides. For example, work on both sides of the centerline that is one station long is to be paid as one station of work, not two. This guidance is to be waived when the specifications or plans are explicitly contradictory. | |||
==109.2 Scope of Payment (for [http://www.modot.org/business/standards_and_specs/SpecbookEPG.pdf#page=4 Sec 109.2])== | |||
Payment to the contractor and the exceptional situations that may affect payment are covered by Sec 109. | |||
==109.3 Compensation for Altered Quantities (for [http://www.modot.org/business/standards_and_specs/SpecbookEPG.pdf#page=4 Sec 109.3])== | |||
Typically this applies to Major Items, which are marked in the Items window of AWP. When there are no major items identified on the job, the greatest cost items on the job, that aggregately add up to 60% of the contract, are defined as the major items even though any one of them does not meet the 10% criteria of a Major Item. | |||
==109.4 Differing Site Conditions and Changes in the Work (for [http://www.modot.org/business/standards_and_specs/SpecbookEPG.pdf#page=4 Sec 109.4])== | |||
Differing site conditions include subsurface or latent physical conditions at the site differing materially from those indicated in the contract, or unknown physical conditions of an unusual nature differing materially from those ordinarily encountered and generally recognized as inherent in the work. Changes in, or extra, work includes items of work not provided for in the contract as awarded, but found essential to the satisfactory completion of the contract. | |||
==109.5 Force Account (for [http://www.modot.org/business/standards_and_specs/SpecbookEPG.pdf#page=4 Sec 109.5])== | |||
When it is impossible to reach agreement on a fair price for necessary extra work having no unit bid prices, the work must be done on a force account basis. This means that the contractor will be reimbursed for the actual cost of labor, insurance and tax, equipment and materials. In addition, the prime contractor will receive specified percentages of these costs to cover supervision, overhead and profit. Contract provisions for this method of settlement are set out in Sec 109.5. Per the specification, the prime contractor will receive an amount equal to five percent of the actual cost of subcontracted work. Actual cost is defined as including the subcontractor’s work, overhead and profit. | |||
Before work is done on a force account basis, a change order must be approved to provide funds and authority for the work. The change order must be supported by the best available estimate of cost. The estimate should be carefully prepared to prevent large variations of actual cost from the estimate. Reference [[:Category:109_Measurement_and_Payment#109.12.1.3_Contingent_Items_-_Settlement_for_Cost|EPG 109.12.1.3]] for more information on how to set up the pay item for Force Account work. | |||
Daily records must be kept during progress of the work. This avoids later misunderstanding about the cost. Keep these records on the [https://epg.modot.org/forms/CM/Force_Account_Spreadsheet.xlsx Force Account Spreadsheet] of the [[:Category:137 Construction Inspection Guidance for Records to be Maintained#137.3 Force Account|Force Account]] Worksheet. An [[media:137 Force Account Worksheet example.xls|example of the force account worksheet]] is available. | |||
===109.5.1 Daily Force Account Record, Labor Account=== | |||
Use the [https://epg.modot.org/forms/CM/Force_Account_Spreadsheet.xlsx Force Account Spreadsheet] of the Daily Force Account Record, Labor Account, as follows: | |||
:In the upper right corner, place the number of the change order that originally authorized the force account work. This will serve to identity all associated reports. If the work is temporary erosion control authorized by order record, use the order record number and initials, O.R. | |||
:Number the report consecutively for each day's work until the operation is completed. Write “Final” after the report number on the last daily report. | |||
:Route, county, and project should be placed in the appropriate spaces. | |||
:Give a fairly detailed description in the space provided for Description of Work. Include the location of the work to be done. Place this data on Report No. 1. It need not be repeated on subsequent daily reports. | |||
::(a) The people employed on the work must be listed daily. This makes it necessary for the contractor to furnish the required information for each employee expected to be used on the work. Separate lines are provided for regular and overtime hours. The hours shown for each employee should be the actual hours worked each day. Separate columns are provided for the rate per hour and the fringe benefit rates per hour. The rates shown should be verified by a copy of the contractor's payroll, if available, or from the contractor's statement required by [http://www.modot.org/business/standards_and_specs/SpecbookEPG.pdf#page=4 Sec 109.5.7]. | |||
::(b) Lead workers, as described under Sec. 109.5.1, must be paid no less than the prevailing hourly wage for the classification they are working in. If a lead worker is salaried, the contractor must provide documentation of the amount actually paid and the hours actually worked. This documentation is required by Sec 109.5.7. Salaried superintendents are not covered by the prevailing wage provisions and should not be included in the labor account. Their expenses are covered by the 20 percent overhead and profit as provided in Sec 109.5.2. | |||
:If actual wage rates and fringe benefits cannot be determined in advance, it will be satisfactory to use rates shown in the contract for each classification. If rates from the contract are used, it will be necessary to obtain the actual rates paid by the contractor and make revised sheets before preparing the [https://epg.modot.org/forms/CM/Force_Account_Spreadsheet.xlsx Force Account Spreadsheet] of the Summary of Costs for the force account work. The contractor’s representatives should sign any revised sheets. | |||
:Total the labor account at the end of each day. Add the previous day's total to get a running total to date. | |||
:Check the appropriate spaces at the bottom of the page to indicate whether there were any materials or equipment charges that day. If the answer in both cases is no, the "Equipment and Materials Account" will not be required for that date. | |||
:On the lower left of the form is space for the signature of the resident engineer, or of the employee designated in writing to sign the daily forms. ALternately, this can be done by attaching a digital signature to the form once it has been changed to a pdf document. | |||
:The employee designated in writing by the contractor shall sign immediately below MoDOT's representative. Insert the name of the contractor below the space for this signature. | |||
:Give the contractor the original and retain two copies. The MoDOT copy may be retained electronically. | |||
===109.5.2 Daily Force Account Record, Equipment and Materials Account=== | |||
Complete this portion of the [https://epg.modot.org/forms/CM/Force_Account_Spreadsheet.xlsx Force Account Spreadsheet] of the Worksheet, if either materials or equipment charges were assessed for the day. Place the same information in the upper right corner as was placed on the Labor Account portion of the Worksheet. The report number is to be consecutive for the Equipment and Materials Form. It need not agree with the number on the Labor Account Form. | |||
The headings for the various spaces under Materials Account are self-explanatory. | |||
Each equipment unit must be listed separately. The contractor must supply information on all equipment to be used on a force account basis. The information must be in sufficient detail to allow accurate determination of the allowable rental rent according to [http://www.modot.org/business/standards_and_specs/SpecbookEPG.pdf#page=4 Sec 109.5.4]. | |||
'''Rental rates on file with the Commission''' are the rates contained in [https://app.equipmentwatch.com/search/by-manufacturer ''Rental Rate Blue Book''] for construction equipment. [[media:Equipment Rental Rates from the Blue Book.doc|Equipment Rental Rates from the Blue Book]] [[image:bulldozer.jpg|20px]] For contractor-owned equipment, apply the Model Year and Region adjustments, then divide the monthly rate by 176 hours to obtain the FHWA approved hourly rate. The listed estimated operating cost per hour is also applied for the time the machine is in use. | |||
In all other cases, the resident engineer should negotiate rental rates with the contractor, subject to approval by the district. Sec. 109.5.4 states, "In no case shall the rental rates exceed those of established distributors or equipment rental agencies.” Proposed rates for contractor owned equipment may not exceed the rate determined by the above paragraph or the rate charged locally by equipment rental companies, whichever is lower. If special cases indicate that higher rates may be justified, send the proposed rates to [http://sp/sites/cm/Pages/default.aspx Construction & Materials] with the district's recommendation and data to support the proposed rates for division review. | |||
Contractor's proposed rates shall be submitted to the resident engineer in writing. The proposal shall state whether the rate includes fuel and lubricants. After district concurrence, the resident engineer shall grant approval in writing. The written proposal and approval make up the agreement. Send both letters to the district with the [https://epg.modot.org/forms/CM/Force_Account_Spreadsheet.xlsx Force Account Spreadsheet] of the Daily Force Account Record, Summary of Costs after the work is done. | |||
When this has been done, use of the various column headings is based on the agreement. The columns for No. Hours, Previous Hours, and Net Hours are self-explanatory. They are to be used regardless of rental basis. | |||
If equipment is to be used on an hourly rental basis, the Hour Rate multiplied by the Rate Adjustment Factor will be used. In all other cases, list the rental on either a weekly or monthly basis as agreed. | |||
When equipment is rented from a recognized rental agency specifically for the force account work, the contractor will normally be allowed the actual rental paid. This must be established by paid invoices. | |||
If contractor-owned equipment must be kept available full time at the site, or if it is specialized equipment for which there is no other use on the project, it may become necessary to allow rental on a full time basis. The unit should then be shown at 8 hours of rental for each day, Monday through Friday, at the hourly rate established as outlined in the [https://app.equipmentwatch.com/search/by-manufacturer Rental rates on file with the Commission] paragraph, above, unless the resident engineer has authorized overtime use of the equipment. If the agreed rate is "bare" rate, the agreed operating cost per hour would be added to the "bare" rate only for actual operating hours. | |||
If contractor-owned equipment is to be used on a part-time basis and will be used for other work on the project, it should be carried on the equipment account at actual hours used. | |||
If equipment must be shipped to the project specifically for force account work, the shipping costs are reimbursable. Such costs should be carried in the equipment account by listing the unit involved and showing the shipping cost under amount. Write in the invoice number, noting it as shipping cost, under the rate headings. | |||
For the time required to move the equipment to and from the site of the ex work and any authorized standby time, the rate will be 50% of the hourly rate after the actual operating costs have been deducted. | |||
===109.5.3 Force Account Record, Summary of Costs=== | |||
The Summary of Costs, [https://epg.modot.org/forms/CM/Force_Account_Spreadsheet.xlsx Force Account Spreadsheet], is prepared in quadruplicate when the force account work has been completed. | |||
On the Summary, place in the upper right corner the number of the original authorizing change order. Complete the description and location of work in considerable detail. | |||
Give the original to the contractor. Retain the fourth copy in the resident engineer's file. Send the other two copies to the district office for checking. | |||
One copy sent to the district office is to be accompanied by a copy of each daily report for checking. The daily reports, after checking, are to be filed with the district copy of | |||
the Force Account Record Summary of Costs. | |||
==109.6 Method of Payment (for [http://www.modot.org/business/standards_and_specs/SpecbookEPG.pdf#page=4 Sec 109.6])== | |||
Contractor payments are made electronically to the contractor’s designated financial institution on the basis of the payment estimate which is created twice a month when work on a contract is active. | |||
Payment estimates must be supported by documentary evidence that work items allowed have actually been done. Evidence may be in the form of scale tickets, diary entries, material receipts, etc. The payment estimate is intended to provide payment to the contractor for all work performed during the estimate period. In no case should payment for work be delayed beyond the estimate period following the period in which the work was performed. | |||
Earthwork quantities may, for example, be supported by load count entries in the inspector's diary. Another way is by diary entries giving limiting stations of completed balances. | |||
Weight or volume tickets are a sound basis for allowing payment on items measured in this manner. | |||
Check all items against inspection records to be sure they are properly approved. | |||
:Provide equitable payment. If work remains to be done (for example, patching the tie holes in concrete) allowance for the appropriate pay item should be reduced. The reduction should be the amount estimated as the cost of completing the work. Make allowance in full for all completed items. | |||
:Items to be paid for by [http://sp/sites/tp/Pages/default.aspx Planning] in connection with weight station complexes are to be included on the regular Engineer's Payment Estimate. At conclusion of this work, a certification is to be submitted with the estimate stating that the scales and material used met specification requirements. | |||
:[http://www.modot.mo.gov/business/contractor_resources/biditemslisting.htm Bid items] not covered in the bid item master list will be indicated in the description block by the term "Miscellaneous" and supplemental number. The resident engineer may insert an abbreviated description using AWP. | |||
:Engineer's Payment Estimates should be submitted for liquidated damages even when no pay items are listed. Such estimates indicate a negative amount due the contractor; accordingly, no payment can be made and no further action is taken. | |||
==109.7 Partial Payments (for [http://www.modot.org/business/standards_and_specs/SpecbookEPG.pdf#page=4 Sec 109.7])== | |||
Partial payments are payments made over the course of the contract each estimate period, and payments made for material allowance. | |||
===109.7.1 Payment Estimates=== | |||
[[:Category:101 Standard Forms#Contractor Pay Estimates|Payment estimates]] [[image:bulldozer.jpg|20px]] are generated by the AWP computer software application. | |||
=== === | '''109.7.1.1.''' Estimates will be generated for all active contracts, regardless of the amount of payment encountered during the estimate period. This includes all estimates for contracts which will produce payment, "no pay" estimates (zero dollar value) and estimates which result in a negative payment. | ||
Should the contract be inactive and a series of estimates will be no pay estimates, a letter or e-mail shall be sent to the contractor with a copy to the controller's office stating estimates will not be generated during the following time periods because there is no work conducted on the contract. The controller's office will record this information and will not contact the Resident Engineer because estimates haven't been generated for a specific time period. | |||
'''109.7.1.2.''' The first level of estimate generation will be designated by the Resident Engineer at the time of contract activation. The Resident Engineer will notify the AWP Administrator who this person shall be. This person must have project manager access to the system. | |||
Progress estimates will be generated for estimate end dates of, generally, the 1st and 15th of each month. The controller's office will issue a chart of estimate due dates annually. AWP estimates must be approved by Level 2 (Resident Engineer) no later than 4:00 PM on the day listed on the chart as "Due in Controller's Office." | |||
'''109.7.1.3.''' Estimates may be generated repeatedly prior to the estimate ending date, in order to resolve discrepancies or check quantities. Two payment estimates shall be made per month for active contracts. The official pay estimates shall be generated with the period ending dates of the 1st and the 15th, making the estimate periods typically the 2nd day of the month to the 15th day, and the 16th day to the 1st of the following month. There may be exceptions to the estimate periods depending upon the financial systems such as the end of the state fiscal year. Other exceptions may be made to the estimate period depending on the status of the contract or as notified otherwise by the AWP Administrator and in the first paragraph of EPG 109.7.1.4, below. | |||
All indexes based upon a monthly index value shall use the same index value for the entire estimate period even though the index value may be reestablished on the 1st of the month. For example the asphalt and fuel index values change on the 1st of the month, but any work completed on the 1st shall use the same index value as the previous month so that the entire 16th to 1st estimate period uses the same index value. | |||
Estimates can be re-generated without deleting the existing estimate from the Estimate History window. Do not use the "delete" option to delete an estimate. To re-generate an estimate for a pay period, just generate that estimate. The system will indicate that an estimate already exists for the period, and will prompt “Would you like to delete?” (meaning to overwrite the existing estimate.) Select "Yes", which will reset the tables and the estimate will be generated containing any new information that has been added. | |||
| [https://epg.modot.org/forms/ | |||
'''109.7.1.4.''' The progress estimate for the period ending July 1 of each year shall be changed by the user to the period ending date of June 30th, prior to estimate generation. This change shall be made to coincide with the MoDOT Fiscal Year End cycle. | |||
Supplemental estimates will not be generated unless specifically instructed to do so by the AWP administrator. | |||
Final Estimates shall be generated by the Resident Engineer prior to submission of the final plans to the District for checking. When logged into the system as a Resident Engineer, only final estimates can be generated. For a Resident Engineer to generate a progress estimate, they must log in as a project manager. | |||
'''109.7.1.5.''' Payment estimates must be supported by documentary evidence that work items allowed have actually been done. Evidence may be in the form of scale tickets, diary entries, material receipts, etc. Earthwork quantities may, for example, be supported by load count entries in the inspector's remarks. Another way is by remarks entries giving limiting stations of completed balances. Weight or volume tickets are a sound basis for allowing payment on items measured in this manner. The payment estimate is intended to provide payment to the contractor for all work performed during the estimate period. In no case should payment for specification compliant and accepted work be delayed beyond the estimate period following the period in which the work was performed. | |||
Check all items against inspection records to be sure they are properly approved. | |||
'''109.7.1.6.''' The Division Final Plans Reviewer shall notify the Resident Engineer when the final estimate is approved and the final plans are passed for payment. Once the Resident Engineer receives the notification, the Resident Engineer will send the prime contractor the Estimate Summary Report(s) for the final estimate as outlined below: | |||
:'''General:''' The Cognos report “Estimate Summary for Contract, By Estimate Number” is the official estimate report to send to the prime contractor on all MoDOT contracts administered through AWP. This will establish the policy and procedure related to this function of AWP. | |||
|- | : Prior to producing this report, it shall be the responsibility of the Resident Engineer to verify the accuracy of the estimate and to approve the estimate in AWP. The Resident Engineer will make this verification by confirming the Last Approver ID is the User ID of the Resident Engineer in the Estimate Summary of each contract. | ||
|- | : After the RE has verified the estimate has been approved at the Resident Engineer level, the Estimate Summary for Contract, By Estimate Number shall be electronically saved as a .pdf file in eProjects. Refer to [[:category:137 Construction Inspection Guidance for Records to be Maintained|EPG 137 Construction Inspection Guidance for Records to be Maintained]] for more information on saving reports produced from AWP or information retrieved from AWP. | ||
| [ | |||
===109.7.2 Material Allowance=== | |||
Under [https://epg.modot.org/forms/CM/AWP_CO_Construction_Stockpiles.doc stockpile materials] should appear those items for which a payment may be made in accordance with the general requirements. Check the specification for the minimum acceptable material allowance. Non-perishable items to be incorporated in the finished product may, in general, be included on the estimate for stockpile materials provided satisfactory inspection reports, certifications or mill test reports and required invoices are in the project file. When the item first appears on the estimate, the resident engineer must have on file a copy of an invoice to substantiate the unit prices allowed. Receipted bills for all materials allowed on the estimate must be furnished to the resident engineer within the time established by specifications, or the item must be eliminated from future estimates. Missouri state sales tax may be included in material allowances if shown on invoices or receipted bills. Each receipted bill must be marked or stamped paid with date of payment shown, as well as the name of the firm and signature of the person who received payment. All invoices and receipted bills obtained to substantiate material allowances during progress of the project are to be filed in the district as part of the permanent project record. | |||
Some aggregates are accepted for "quality only" at the point of production. Total acceptance is not made at the time of production because additional processing and/or screening are required before incorporation into the final product. If gradation tests, which are run for information purposes only, indicated it is reasonably possible to produce an acceptable finished product, this material may be included in the stockpile material payment. | |||
If test reports or visual inspection on the above material or other material that might be produced and accepted indicate that it will be unsatisfactory at a later date due to gradation, excess P.I., segregation, contamination, etc., these materials should not be included on the stockpile materials payment. | |||
The price per unit for material produced by the contractor or by a producer other than an established commercial producer should reflect the actual cost of production. The units shown under material estimate should be the same unit of measure used in the bid item where possible, such as pound for steel, linear foot for piles, etc. Where this is not possible, a convenient unit such as ton for aggregate should be used. Quantities in excess of contract requirements should not be allowed. Hauling costs should not normally be included in the unit cost of any material unless it has been hauled to a site where it can immediately be incorporated in the finished product or work. If hauling cost is allowed, it must be considered with relation to the value of the material in case it is necessary for the state to take it over. Stockpiling costs are not to be included as part of the unit cost. | |||
Items that are to be accepted by project personnel must be inspected and found satisfactory prior to being included on a stockpile materials payment. Quantities for materials included on a stockpile materials payment should never exceed approved quantities. | |||
Before an allowance will be approved for payment on material stockpiled or stored on private property, or for aggregates stored on property operated as a commercial business, a lease agreement from the contractor or subcontractor showing compliance with the following points must be submitted to the district office for approval. | |||
:'''1.''' A complete land description covered in the lease form and the haul distance from the lease area to the project. | |||
:'''2.''' The following statement included in the lease agreement: | |||
:"It is understood and agreed by the parties hereto that the land herein involved is to be used as a materials storage site and that the prime contractor, whether or not the lessee herein, may obtain payment from the Missouri Highway and Transportation Commission for material stored thereon". | |||
:"It is further understood and agreed by the parties hereto that the prime contractor or contractor having a written agreement with the Missouri Highway and Transportation Commission for the construction of highway work involving this lease and the materials stored thereon, whether or not the lessee, and the employees of the Missouri Highway and Transportation Commission shall have the right of access to the property covered by this lease at all times during its existence and that in the event of default on the part of the lessee or the prime contractor, if other than lessee, the Missouri Highway and Transportation Commission may enter upon the property and remove said materials to the extent to which advance payments were made thereon". | |||
:An area leased on property operated as a commercial business must be posted so as to divorce the site for stockpiling of highway materials from the commercial operation. | |||
:If either party to the lease agreement is incorporated, it is essential that an Acknowledgment by Corporation be attached for each corporation involved since an individual cannot legally bind a corporation without duly enacted authorization by the corporation's Board of Directors. A suitable form for this purpose is shown in ''Agreement for Shifting State Highway Entrance'', page 1. Other forms may be used by some corporations and are acceptable if they fulfill the intent of the form illustrated. Leases involving corporations should not be accepted without the Acknowledgment. | |||
:Signatures by individuals must be notarized, or be witnessed by at least two disinterested persons. The address of witnesses should be shown. | |||
:When material is stored on property owned by a railroad and is accessible by a public roadway, it is not necessary to obtain a lease agreement to permit this material to be placed on the estimate as a stockpile material. | |||
:If hauling charges are to be included as part of the cost of materials allowed for payment, invoices for hauling charges must be provided by the contractor in the same manner as invoices for the material. An exception to this requirement is allowance for the cost of the rail freight. For rail freight the contractor should supply a copy of the first freight bill to substantiate the freight rate. In lieu of submitting receipted freight bills, the contractor may then sign a statement on each material invoice indicating that freight charges have been paid. If the contractor prefers, a letter may be submitted listing several invoices and indicating freight charges that have been paid. Whichever procedure is adopted, the resident engineer must be assured that freight charges have been indicated as paid for all materials invoices submitted to verify quantities. | |||
:The engineer may also include in any payment estimate an amount not to exceed 90 percent of the invoice value of any inspected and accepted fabricated structural steel items, structural precast concrete items, permanent highway signs, and structural aluminum sign trusses. These items must be finally incorporated in the completed work and be in conformity with the plans and specifications for the contract. These items may be stored elsewhere in an acceptable manner provided approved shop drawings have been furnished covering these items and also provided the value of these items is not less than $25,000 for each storage location for each project. | |||
:The engineer may also include in any payment estimate, on contracts containing 100 tons or more of structural steel, an amount not to exceed 100 percent of the receipted mill invoice value of structural carbon steel or structural low alloy steel, or both, which is to form a part of the completed work and which has been produced and delivered by the steel mill to the fabricator. | |||
While the nature and quality of material is the contractor’s responsibility until incorporated into the project, material presented for stockpile materials payment must be inspected prior to being approved for payment. The nature of that inspection is at the discretion of the engineer and may include sampling and testing to determine whether the material has a reasonable potential of compliance, once incorporated into the project. This sampling and testing may occur wherever the material is offered for stockpile materials payment, including stockpiles in quarries and at other off-project sites. Material that is a component of a mix may be compared to the associated mix design or to any other specification criteria that may apply. | |||
==109.8 Final Acceptance and Payment (for [http://www.modot.org/business/standards_and_specs/SpecbookEPG.pdf#page=4 Sec 109.8])== | |||
In addition to confirmation of final quantities, all other adjustments to the contract amount should be reviewed and verified prior to making final payment to the contractor. See [[:Category:105 Control of Work#105.15.2 Final Acceptance|EPG 105.15.2]] for guidance on the Final Acceptance process. | |||
'''[https://epg.modot.org/forms/CM/Contractors_Affidavit_C-242.pdf Contractor's Affidavit Regarding Settlement of Claims (C-242)]''' | |||
'''[https://epg.modot.org/forms/CM/Contractors_Affidavit_C-242_With_Exceptions.pdf Contractor's Affidavit Regarding Settlement of Claims (C-242) with Exceptions]''' | |||
'''Addressing claims from creditors (e.g. supplier, sub, etc.) against the prime contractor:''' | |||
Intervening in pay disputes between the prime and their creditors should be limited to facilitation efforts by the RE. The RE should contact the prime, discuss details of the payment issue, and advise of Missouri’s Prompt Payment Law if there is not a valid reason for their delay in payment. If no resolution can be facilitated, provide the creditor with the Surety’s name and contact information, as listed in the contract bond. Also, note the name and nature of the dispute for a reference when the C-242 is received at the completion of the job. Pay retainage should not be withheld from the estimate because of a creditor claim. Payments should not be made to the Surety unless the contract is declared to be in default and the Surety submits a formal letter requesting all future contractor payments go directly to them. If the dispute is not resolved prior to the [[:Category:105 Control of Work#105.15.1.4 Acceptance for Maintenance (Final Inspection)|Final Inspection]], provide the contractor with the [https://epg.modot.org/forms/CM/Contractors_Affidavit_C-242_With_Exceptions.pdf Contractor's Affidavit Regarding Settlement of Claims (C-242) with Exceptions] form so that they can list all pay disputes and state the reason why full payment was not made. Contact the Division of Construction and request authorization to close out the job despite the unsettled claim(s). Projects will typically be authorized for closure unless the dispute is deemed to directly involve the Commission. If the pay dispute involves a Disadvantaged Business Enterprise (DBE), advise External Civil Rights of the details surrounding the dispute. | |||
==109.9 Retained Percentage (for [http://www.modot.org/business/standards_and_specs/SpecbookEPG.pdf#page=4 Sec 109.9])== | |||
Formal retainage is no longer designated by MoDOT as a routine part of the contract however [https://revisor.mo.gov/main/OneSection.aspx?section=34.057 34.057 RSMo] does allow up to 10% of the contract price to be retained in order to ensure performance of the contract. Payment may be withheld on any particular work item that has not been completed in accordance with the contract. This can include work incidental to the work item, and required documentation directly related to the work. | |||
==109.10 Contract Assignment Process - Contract Reassignment to a New Contractor (for [http://www.modot.org/business/standards_and_specs/SpecbookEPG.pdf#page=4 Sec 109.10])== | |||
The Missouri Highway and Transportation Commission (MHTC) and MoDOT advertise construction projects, open bids and award several hundred contracts each year. Typically, the awarded contractor performs the work, with subcontractors, through completion and the contract is closed out. Sometimes contractors may be purchased by other contractors, may have taken on too much work, or decide for other reasons not to finish a contract they were awarded, and then wish to make an arrangement with another contractor to complete the project(s) under the same contract conditions. MoDOT has prepared for this slight possibility with a process for transferring the contract to a new prime contractor by reassigning the contract through an “Assignment Agreement”, subject to consent and approval by the MHTC. [http://sp/sites/cc/Pages/default.aspx Chief Counsel's Office] has created [[153.7 Construction and Materials|template assignment agreements for the typical scenarios]]. [http://sp/sites/cm/Pages/default.aspx The Construction and Materials Division] is responsible for working with the contractors to process the assignment agreement allowing the new contractor to work on the project and collect payment from MoDOT. | |||
Although the original contract remains in place, the assignment agreement assigns responsibilities for completing the contract to the new contractor. MoDOT does not pay any additional compensation to the contractor when agreeing to an assignment, nor does either contractor pay MoDOT any compensation for the transfer. The original contractor (assignor) and the new contractor (assignee) have their own agreement regarding this transaction which sometimes includes transferring other assets from one contractor to the other. MoDOT is only concerned with continuing surety protection while the work is still active and completing the contract on time and within budget. MoDOT and the MHTC could object to a transfer, but the likely outcome is a situation where the original prime contractor has been purchased, has no assets remaining and their surety would have to be engaged to complete the work. Therefore, consenting to the assignment is generally in the best interest of all involved parties and likely the best way to get work completed in these situations. | |||
Once a contract is reassigned, the new contractor (assignee) is the responsible contractor that MoDOT expects to and is contractually obligated to complete the work, will be paid for work completed and will be held accountable to finish the contract on time and within budget. MoDOT will change the information in the contract administration system to recognize the new contractor and the Resident Engineer’s office will be notified of the changes. See the [[media:109.10 transfer.xlsx|Assignment Matrix]] for the details of the reassignment process. | |||
==109.11 Compensation for Project Delays (for [http://www.modot.org/business/standards_and_specs/SpecbookEPG.pdf#page=4 Sec 109.11])== | |||
Sec 109.11 designates the conditions for which compensation may be appropriate to cover the cost of a project delay. Review the specification and refer any questions to the [http://sp/sites/cm/Pages/default.aspx Construction and Materials] Division. | |||
===109.11.1 Documentation of Delay Costs=== | |||
When a delay has been determined to be compensable (that is, it was directly caused by the Commission), and the contractor has claimed impact costs due to the delay, reference Sec 109.11.1 for a list of eligible delay costs. An additional 10% is added to the sum of these costs to account for home office overhead and all other costs. The total of all costs, plus the 10% mark-up, should be summarized on a Documentation Record as supporting documentation for the lump sum delay cost change order. The Force Account spreadsheet should not be used as those accounting methods are only for added work and include other mark-up rates for profit and overhead. | |||
There are four categories for additional costs. Below further clarifies what is included in each of these items. | |||
:'''(a) Non-Salaried labor expenses. ''' This is most commonly for trade workers who are compensated on an hourly rate. This would be for workers such as laborers, carpenters, iron workers etc. During a delay there may be activities that need to still be ongoing. This would include activities such as traffic control and erosion control. Salaried workers are non-compensable. These workers can be reassigned to other projects or perform other activities. Their salary is ongoing and would be incurred regardless of the delay. Labor rate increases are allowed. For example, paving was to be performed in October and due to the delay, it could not be performed until May. A labor rate increase went into effect in January. Therefore, the net labor increase for the hours worked on the paving would be allowed. This does not apply to increases in prevailing wage rates as the original wage order remains in effect for the life of the project. The only mark-up for labor costs, prior to the 10% overall markup, should be inclusion of additives for insurance and taxes (FICA/FUTA/SUTA/General Liability/Work Comp). | |||
:'''(b) Material costs.''' This is for an increase in costs for materials due to the delay. Actual documented increases in costs for materials due to the delay is allowable. For example, a bridge deck scheduled to be poured in October is now being poured in March due to the delay. The concrete price was increased in January. Therefore, the net increase in concrete material cost is allowed. | |||
:'''(c) Equipment costs.''' This is the cost of on-site equipment that is idled. It would not include trucks or other mobile equipment that can readily be relocated. The reimbursement method is outlined in detail in Sec 109.11.2. | |||
:'''(d) Costs of extended job-site overhead.''' These are ongoing costs such as the job site office, porta-potty rental, utilities, dumpster rental etc. that are extended due to the delay. (It does not include cell phone costs which are portable and not tied to the project.) These costs are only compensated for the period from the original completion date to the extended completion date as a result of the delay. This applies even if the contractor’s submitted schedule indicates they would have completed the project before the original completion date (since there is no guarantee that the project would have been completed ahead of the original completion date). | |||
===109.11.2 Calculation of Equipment Delays=== | |||
Equipment costs should be limited to on-site equipment that remains inactive due to the compensable delay. In lieu of computing actual ownership cost of the equipment, the Non-Active Use Standby Rate, as published in ''EquipmentWatch'', shall be used to calculate the costs of idle equipment owned by the contractor. Multiply the hourly standby rate by 8 hours for each full weekday/non-holiday elapsed during the delay. If the delay extends for a month or more, use 176 hours/month. For rented equipment, payment will be made per the actual rate in the rental agreement. | |||
'''Long-Term Delays''' | |||
If the delay is anticipated to be long-term, such that the projected delay cost would exceed the cost to mobilize the equipment from/to the job site, the Resident Engineer should inform the contractor in writing that they have the option to mobilize the equipment off-site for use elsewhere. State the earliest possible date resumption of work is anticipated. Clarify that payment for equipment standby costs will be made only from the start of the delay period through the date of the notice of the long-term delay. If the contractor chooses to mobilize the equipment off-site, actual mobilization costs from/to the site will also be paid. If the contractor chooses to leave the equipment on-site, no standby costs for equipment will be paid past the date of the Resident Engineer's notice. | |||
===109.11.3 Common Claims=== | |||
No other overhead costs are reimbursable. See Sec 109.11.3 for a list of common claims that are contractually ineligible. | |||
==109.12 Change Orders== | |||
The primary purpose of a change order is to document a supplemental change to the contract. The official definition, as stated in [https://www.modot.org/missouri-standard-specifications-highway-consthction Sec 101], is as follows: | |||
:'''Change Order''' - ''A written order from the engineer to the contractor, as authorized by the contract, directing changes in the work as made necessary or desirable by unforeseen conditions or events discovered or occurring during the progress of the work.'' | |||
The second most primary purpose of the change order process is to ensure proper authority has been granted before proceeding with revisions in quantities or changes in scope of work, design concept, time or specifications. Changes in scope should be limited to the original intent, purpose and limits (length and width) of the job. In instances where proposed changes in scope go beyond these original job parameters, the change order shall be considered a major change order (Sequence 4). Significant scope changes require the State Construction and Materials Engineer to discuss the requested changes with the Asst. Chief Engineer prior to granting approval. | |||
Change orders must have approval at all required levels before the work proceeds. Exceptions are granted for routine or minor changes, or emergency revisions for which verbal approval has been granted. In rare cases it may be necessary to proceed with emergency measures without prior approval. In such cases, verbal approval should be sought as soon as practicable. Indicate in the DWR remarks the name of the individual who provided verbal approval. For change orders that provide payment for additional work, all attempts should be made to complete the process promptly so that the contractor can be compensated at the end of the pay period in which the work was performed. | |||
'''Environmental Change Orders''' - Any design changes that include disturbance of new areas on the project, or that include any other unplanned environmental impacts, should be reviewed by the Project Manager to determine if a request for environmental services is necessary prior to implementation. | |||
'''Job Order Contract Change Orders.''' Job Order Contracts have unique contract terms that limit spending to a budgeted amount and often include pre-approved time extensions. Reference [[147.3 Job Order Contracting (JOC)#147.3.9 Change Order Approvals|EPG 147.3.9 Change Order Approvals]] for additional guidance on administration of change orders for Job Order Contracts. | |||
===109.12.1 Change Order Preparation=== | |||
Change orders are generated in AWP, and subsequently displayed in pdf format using the appropriate Cognos change order form. Quick Reference Guides are provided below to provide details. All completed change orders and supporting documentation shall be in electronic format and stored in eProjects. Change orders shall be transmitted in the original electronic format and shall not be scanned. Ink-signed paper copies or scans from a contractor shall not be accepted. A QRG ([https://epg.modot.org/forms/CM/Digital_Signature_for_Adobe_Reader_DC_or_Pro_DC.docx Digital Signature for Adobe Reader DC or Pro DC]) is available to assist contractors with creation of their digital ID, and registration of that ID with MoDOT. The contractor shall also inform the RE in writing who they authorize to approve change orders on their behalf. | |||
'''Supplemental Documents.''' Supplemental contract documents that are pertinent to the change order directive, such as new or revised plan sheets, new or revised Job Special Provisions, revised cross-sections, etc., shall be merged with the change order form to create a single file in pdf format and saved to eProjects prior to sending to the contractor. | |||
<div id="Supporting Documentation."></div> | |||
'''Supporting Documentation.''' Any pertinent supporting documents (e.g. Contingent Item Price Check form, relevant emails, letter of agreed price, computation sheets, mock Force Account computations, etc.) that provide additional details of the change, or provide justification of a price for contingent work, should be saved in eProjects as Supporting Documentation. All supporting documents should be merged into a single pdf document for each change order (the Force Account spreadsheets will require conversion to pdf format). At a minimum, any change order that contains a new contingent item should have supporting documentation that justifies the agreed price. More information on how to justify an agreed price can be found in [[#109.12.1.3 Contingent Items - Settlement for Cost|EPG 109.12.1.3 Contingent Items - Settlement for Cost]]. Time adjustment change orders require supporting documentation (e.g. weighted time-table computation, analysis of how an excusable delay impacted the critical path, negotiated settlement narrative, etc.), unless the change order reason is self-explanatory. | |||
'''Final Change Order.''' If a clean-up change order is necessary after project completion to adjust the quantity of one or more pay items to the final accepted amount, this is designated as the “Final” change order. If no final change order is necessary due to all quantities being updated to final status by previous change order(s), the contractor should be informed that records indicate no further quantity adjustments are needed and the project will be closed out, as is, with current quantities as listed on the most recent pay estimate. | |||
The following Quick Reference Guides provide detailed information on how to create a change order in AASHTOWARE Project and how to create the contractual pdf form: | |||
::* [https://epg.modot.org/forms/CM/AWP_CO_1ChangeOrderOverview.doc AWP CO 1 Change Order Overview] | |||
{|style="padding: 0.3em; margin-left:7px; border:2px solid #a9a9a9; text-align:center; font-size: 95%; background:#f5f5f5" width="300px" align="right" | |||
|- | |||
|<center>'''Change Order Examples'''</center> | |||
|- | |||
|[[media:109.12.1 Mobilization.pdf|Adjust Mobilization for Contract Bond]] | |||
|- | |||
|[[media:109.12.1 Chief Engineer.pdf|Chief Engineer Level]] | |||
|- | |||
|[[media:109.12.1 Division.pdf|Division Level]] | |||
|- | |||
|[[media:109.12.1 RE.pdf|RE Level]] | |||
|- | |||
|[[media:109.12.1 Time.pdf|Time Extension]] | |||
|} | |} | ||
=== === | ::* [https://epg.modot.org/forms/CM/AWP_CO_2ChangeOrderAddingNewItemorOverrunUnderrunExisting.doc AWP CO 2 Change Order Adding New Item or Overrun/Underrun of Existing Items] | ||
::* [https://epg.modot.org/forms/CM/AWP_CO_3ChangeOrderTimeExtension.doc AWP CO 3 Change Order Time Extension] | |||
{| | ::* [https://epg.modot.org/forms/CM/AWP_CO_4ChangeOrderValueEngineering.doc AWP CO 4 Change Order Value Engineering] | ||
::* [https://epg.modot.org/forms/CM/AWP_CO_5ChangeOrderNoCostContractModification.doc AWP CO 5 Change Order, No Cost Contract Modification] | |||
::* [https://epg.modot.org/forms/CM/AWP_CO_6ChangeOrderMobilizationAndContractBond.doc AWP CO 6 Change Order, Mobilization and Contract Bond] | |||
::* [https://epg.modot.org/forms/CM/AWP_CO_7ChangeOrderApproval.doc AWP CO 7 Change Order Approval] | |||
::* [https://epg.modot.org/forms/CM/AWP_CO_Change_Order_Codes.doc AWP CO Change Order Codes] | |||
::* [https://epg.modot.org/forms/CM/AWP_CO_Change_Order_Reports.doc AWP CO Change Order Reports]. | |||
====109.12.1.1 Change Order Approval Level Criteria==== | |||
This article provides the criteria to determine the required approval level of a change order. AWP assigns a sequence number to correspond with each approval level, as follows: | |||
::Contractor level (Sequence 1) – Approval applied in AWP by the Construction Project Office Assistant. | |||
:'''Non-major Change Orders:''' | |||
::RE level (Sequence 2) | |||
::District level (Sequence 3) | |||
:'''Major Change Orders:''' | |||
::Division level (Sequence 4) | |||
::Chief Engineer/ Chief Financial Officer level (Sequence 5) | |||
:FHWA Review (Sequence 6). If a project is designated for federal involvement for change orders on the PODI Matrix, and the change order is classified as district level or higher (i.e., Sequence 3, 4 or 5), review and approval by the Federal Highway Administration (Sequence 6) is required. RE level change orders do not require FHWA review. | |||
The change order approval level criteria are listed below and [https://epg.modot.org/forms/CM/Chg_Ord_Approval_Level_Chart.pdf available here in table form]: | |||
{|style="padding: 0.3em; margin-left:10px; border:2px solid #a9a9a9; text-align:center; font-size: 95%; background:#f5f5f5" width="370px" align="right" | |||
|- | |||
|<center>'''[https://epg.modot.org/forms/CM/Chg_Ord_Approval_Level_Chart.pdf Change Order Approval Level Determination Chart]'''</center> | |||
|- | |- | ||
|align="left"|This chart is a graphic presentation of the criteria stated in [[#109.12.1.1 Change Order Approval Level Criteria|EPG 109.12.1.1]]. All change orders require approval in AWP at Project Office Assistant role on behalf of the contractor (Sequence 1) AND the Resident Engineer role (Sequence 2). If the change order exceeds any of the criteria displayed in this chart, it would also need to be approved at the additional Sequence(s) shown. The chart values are absolute values. The criteria that requires the highest sequence approval always prevails over other criteria. | |||
| | |||
| | |||
|} | |} | ||
'''Non-major change orders (Change Order Sequence 2)''' approved by the Resident Engineer are: | |||
:1. Any no-cost (zero dollar) change orders (used when the direct substitution of a particular line item with a contingent item does not generate an additional cost or cost reduction). | |||
:2. Any change in a contract or contingency item less than $50,000. | |||
'''Non-major change orders (Change Order Sequence 3)''' that require approval from the district office, and by FHWA on projects designated for federal involvement on change orders on the PODI Matrix, are: | |||
:1. Any change in a contract item or contingency item from $50,000 to $100,000. | |||
:2. Any new contingency item from $50,000 to $100,000. | |||
'''Major change orders (Change Order Sequence 4)''' that require approval from the division office, and by FHWA on projects designated for federal involvement on change orders on the PODI Matrix, are: | |||
:1. Any change in a contract or contingency item greater than $100,000. | |||
:2. Any new contingency item greater than $100,000. | |||
:3. Any specification change. | |||
:4. Any revision in a contract unit price. | |||
:5. Any change in a “Major Item” greater than 25% from the original contract amount for that line item (in dollars). A Major Item is defined in Sec 101 as, “having an original value in excess of 10% of the original contract amount.” | |||
:6. Any change of the contract amount greater than 25% of the original contract bid amount (also in dollars). | |||
:7. Any change in design concept. | |||
:8. Any change order not approved by the contractor. | |||
:9. Any change order for adjustments due to differing site conditions or significant changes in the character of the work. | |||
:10. All value engineering change orders regardless of cost. | |||
:11. Any change order granting a time extension. | |||
'''Chief Engineer/Chief Financial Officer change orders (Change Order Sequence 5)''' meeting any of the three following criteria must have the concurrent approval of the Chief Engineer and the Chief Financial Officer, and FHWA approval for projects designated for federal involvement on change orders on the PODI Matrix: | |||
:1. Additions greater than 50% if the original contract amount was $500,000 or less. | |||
:2. Additions greater than 25% if the original contract amount was greater than $500,000. | |||
:3. Additions greater than $1,000,000. | |||
====109.12.1.2 Description and Reason for Change==== | |||
The author of the change order should provide sufficient narrative to explain both the reason the change is needed and a description that clearly states any necessary contractual language to define the terms. Enough detail should be included to explain the circumstances to someone who may be unfamiliar with the issue, such as a reviewer or auditor. For contingent items, check to ensure controlling specifications are available that adequately define the work, including the method of measurement and basis of payment. Add any terms not covered by specifications or other contract language. For significant quantity changes, explain exactly what caused the overrun or underrun (e.g. grade change, incorrect shrinkage factor, error in Summary of Quantities, roadway width differed from typical section, additional asphalt needed due to excessive rutting, etc.). Slight quantity variations can be explained as “Final measured quantity, within normal tolerance". | |||
====109.12.1.3 Contingent Items - Settlement for Cost==== | |||
When a MoDOT standard bid item exists for contingent work, use the item number and description from the [https://www.modot.org/bid-items-listing Bid Items Listing]. Miscellaneous “99” numbers are available in this listing for items that require a unique description. | |||
If payment is to be made by force account settlement, use item number 109.4000 FORCE ACCOUNT, enter $1.00 for the unit price and set the quantity equivalent to the estimated cost. The quantity will be adjusted after the work is complete to reflect the actual cost, as determined by the force account summary. | |||
A “Settlement for Cost” statement should be included in the Description and Reason for Change field for all new contingent items. Changes to contract pay items, or previously established contingent items, do not require this statement since the contract prices govern. The “Settlement for Cost” statement, when required, should refer to the basis of settlement (i.e., agreed unit price, a fixed price listed in Standard Specifications, or [https://epg.modot.org/forms/CM/Force_Account_Spreadsheet.xlsx Force Account]). The settlement statement should also state the unit price. Here are some examples of “Settlement for Cost” statements: | |||
:* “Settlement for cost of REPAIRING CONCRETE DECK (HALF-SOLING) shall be made at the agreed price of $69 per square foot.” | |||
:* “Settlement for cost of CLASS 2 EXCAVATION IN ROCK shall be made at $170 per cubic yard, as specified in [https://www.modot.org/missouri-standard-specifications-highway-construction Sec 109.16 Fixed Cost Items].” | |||
:* “Settlement for cost for FORCE ACCOUNT-MODIFY EXISTING DRAIN GRATES, as specified herein, shall be made per Sec 109.5 Force Account Computation.” | |||
'''Justification of Agreed Price.''' Any contractor-proposed price for a contingent item shall be fully evaluated to ensure it is fair and reasonable before accepting it as the agreed price. Justification of the agreed price on any new contingent item shall be documented in eProjects as [[#Supporting Documentation.|Supporting Documentation]]. Documentation is typically made on the [https://epg.modot.org/forms/CM/Contingent_Item_Price_Check.pdf Contingent Item Price Check] form by comparing the agreed price to the Average Unit Bid Prices (BidTabs), or to a price for the same type of work on another area project. Sometimes documentation can be as simple as saving an email string that states the reason the price was deemed acceptable. For unique work for which no price comparison exists, or there are other factors that greatly affect the price, a detailed cost estimate (materials/equipment/labor) should be requested from the contractor that supports their proposal. If the RE concurs that the contractor’s breakdown of costs is reasonable, the price can be accepted. Another tool to arrive at an agreed price, especially for lump sum price quotes, is for project office staff to perform a mock [https://epg.modot.org/forms/CM/Force_Account_Spreadsheet.xlsx Force Account] analysis using anticipated materials, equipment and labor costs. If that total is reasonably close to the contractor’s proposal, the price can be accepted as an agreed price without invoking the force account process. If a price agreement cannot be reached, the RE should direct the contractor to proceed with the work under Force Account Computation per Sec 109.5. | |||
All contingent work must be clearly defined (i.e., include a description of work, material requirements, construction requirements, method of measurement and basis of payment). References to the standard specifications may be used when available. | |||
'''Settlement Clause''' (used only for settlement of a Claim or Controversy, as defined in Sec 101). When a change order involves a negotiated settlement and final resolution of a contentious issue, in order to clarify the settlement is all-inclusive for any associated claims for costs, the following language is recommended for insertion into the change order description: | |||
:''"The amount being paid to <Construction Company> in this Change Order represents a negotiated settlement and, as such, reflects payment of all claims of <Construction Company> and/or any of its subcontractors and suppliers direct and indirect, including all impacts starting from the date of execution of the contract until the execution by both parties of the Change Order. However, nothing in this Change Order affects <Construction Company>'s right to file a claim based on an occurrence after the date of this Change Order."'' | |||
:Note: Delete the last sentence if the change order is being issued after all work on the project is complete. | |||
===109.12.2 Change Order Approval=== | |||
'''Preview for Sequence 3, 4 or 5 Change Orders.''' All draft Major change orders shall be submitted to the to the Construction Liaison Engineer for initial review prior to submitting to the contractor. Likewise, all district level change orders shall be sent to the DCE prior to submitting to the contractor. This is only considered initial approval, change orders sent to the contractor should not contain any MoDOT approval signatures. MoDOT approval and signing shall occur after the contractor digitally signs the change order. | |||
Following any required previews, the RE will submit the completed change order to the contractor as an attachment to an email. The contractor’s signature should be requested on all change order. If the contractor refuses to sign a change order, their refusal should be documented and disclosed to any subsequent approvers (i.e., district or division level approvers). If the decision is made to execute the change order without the contractor’s signature, all other approval signatures will be applied, and the executed change order will be sent back to the contractor as a directive to proceed with the change in work. If the unsigned change order includes new contingent item work, and no contract price or fixed price exists, payment for that portion of the work will need to be designated force account. | |||
Once the digitally signed change order is returned from the contractor, the RE shall upload it to eProjects, sign, and then approve in AWP. For change orders that require district level or higher approval, the RE will then send an email to the District Construction Engineer with a direct link to the change order, along with a link to any supporting documentation. If the change order requires division level approval, the RE should also copy the Construction Liaison Engineer. After approval has been completed at the district level, the DCE will forward the email on to the Construction Liaison Engineer if division level approval is required. The highest-level approver will reply to the RE confirming that the pdf is signed and the change order is approved in AWP. For PODI projects that are designated for change order review by FHWA, the highest-level approver will forward the email on to the appropriate FHWA Transportation Engineer and copy the RE. The FHWA Transportation Engineer will reply to all when approved. | |||
===109.12.3 Time Adjustment Change Orders=== | |||
All time adjustment change orders, whether for overall contract time, individual project time, or specified milestones (e.g. road/bridge closure), are considered major change orders and shall be reviewed and approved by the division office. Initial review by the Construction Liaison Engineer shall be made prior to any agreements with the contractor and prior to submitting the Time Adjustment change order to the contractor. Time adjustments are granted for events deemed by the engineer as excusable delays that inhibit progress of a controlling item of work (i.e., critical path schedule). [https://www.modot.org/missouri-standard-specifications-highway-construction Sec 108.14.1] lists some of the common events that warrant consideration. [[:Category:108 Prosecution and Progress#108.7 Contract Time for Completion of the Work|EPG 108.7 Contract Time for Completion of the Work]] provides guidance for determining the appropriate amount of a time extension. The [https://epg.modot.org/forms/CM/AWP_CO_3ChangeOrderTimeExtension.doc AWP CO 3 Change Order Time Extension] provides guidance on how to generate the time change in AWP. Justification for the extension should be documented and saved in eProjects as [[#Supporting Documentation.|Supporting Documentation]] unless the change order reason is self-explanatory. | |||
All time extension change orders should include a description and reason and for granting of additional time, the amount of days, and any terms associated with the extension. The description should identify the controlling item of work that was affected by the delay, as confirmed by examining the critical path schedule. If the extension includes multiple causes of delay, each cause should be listed separately, along with the amount of time granted for each, excluding any overlap. Time adjustments are sometimes granted for reasons unrelated to an excusable delay. Time adjustments are sometimes granted as part of a negotiated settlement and may not directly correlate with the progress schedule. Regardless of the reason for the extension, a revised Progress Schedule should be requested following execution of the change order. An [[media:109.12.1 Time.pdf|example Time Adjustment Change Order]] is available. | |||
The following statement is recommended for inclusion in all time adjustment change orders to make clear that the additional time being granted includes all excusable delays up to the date of the change order: | |||
:''“This revised Completion Date (or, “This addition of Calendar Days”), as specified, is full and final adjustment for all time and costs, loss or damage including, without limitation, delays, accelerations, or inefficiencies, resulting from the above causes, and is made without prejudice to the Commission.”'' | |||
====109.12.3.1 Excusable Delays for Unusual Events==== | |||
Per [https://www.modot.org/missouri-standard-specifications-highway-construction Sec 108.14.1], the engineer may grant an excusable delay for unusual or extreme events. To qualify, the events must be highly unusual and not just somewhat out of the ordinary. For example, a wet construction season due to above average rainfall does not necessarily constitute “unusually severe weather”. In addition, the event must be outside of the contractor’s control and must have adversely affected the project's identified critical path schedule. Completed work damaged or destroyed by motorist or other outside parties may qualify as an excusable delay only if the remediated work adversely affects the project's critical path. When significant defects or failures in the contractor’s workmanship are discovered during the project and the remediation is extensive and results in significant time delays to the project's critical path, the State Construction and Materials Engineer may, at the State Construction and Materials Engineer's discretion, grant the contractor additional time to perform the remediation as part of a settlement agreement. The contractor shall submit in writing to the State Construction and Materials Engineer a justification request for the additional time. The justification must include the duration and timeframes to complete the remediation. In addition, an action plan that outlines the specific remediation shall be included with the justification. Only the time to perform remediation repairs will be considered for the additional time requests. The decision to grant additional time for these events are the sole discretion of the State Construction and Materials Engineer. | |||
====109.12.3.2 Description, Reason and Supporting Documentation==== | |||
The Description/Reason narrative of the time adjustment change order, as well as the Supporting Documentation, should address four primary areas: | |||
:'''1. Describe the Contract Change -''' Begin by explicitly describing the change in contract terms. For example: ''“The number of Calendar Days for J4P2168, as stated in Section 2.1 of JSP B. CONTRACT LIQUIDAGED DAMAGES, is hereby increased from 130 days to 134 days.”'' Or, if the contract completion date is being extended, state: ''“The Contract Completion Date stated in Section 2.0 of JSP B. CONTRACT LIQUIDAGED DAMAGES, is hereby extended from Nov. 1, 2021 to Nov. 5, 2021.”'' If extensive changes are being made to the JSP, rewrite the JSP as desired, then merge it with the change order and state the following: ''“Delete JSP B. CONTRACT LIQUIDAGED DAMAGES and substitute with the attached version.”'' | |||
:'''2. Justification -''' Now explain the justification for the extension. For example: ''“The major operation, storm sewer pipe installation, was halted from March 15 thru March 18, both dates inclusive, to allow for the relocation of an unexpected water main owned by the City of Lee’s Summit, right of Sta 156+22. Per Sec 105.7.6.1, this delay is considered excusable but non-compensable.”'' If there are many details, provide those in the Supporting Documentation rather than the change order itself. | |||
:'''3. Full and Final Closure Statement -''' Insert our standard closure statement so that it is clear that this agreement is full and final. No additional cost adjustments will be made except for any terms that may have been included in the opening contract change statement. Insert the closure statement (cut/paste) exactly as it is written in [[#109.12.3 Time Adjustment Change Orders|EPG 109.12.3 Time Adjustment Change Orders]]. Just edit the part in parenthesis to match what type of time change you made (i.e., calendar days or date). | |||
:'''4. Supporting Documentation -''' Now provide Supporting Documentation, if necessary. This is an internal document to help reviewers and auditors understand the details. In the simple example above, everything was addressed in the change order itself, so no supporting documents would be needed. But, for example, had a weighted time table calculation been necessary, it would be shown in the Supporting Documentation. Or, perhaps a brief analysis of the critical path schedule is necessary to explain how the number of days granted was derived. | |||
==109.13 Prompt Payment to Subcontractors and Suppliers (for [http://www.modot.org/business/standards_and_specs/SpecbookEPG.pdf#page=4 Sec 109.13])== | |||
Prompt payment of subcontractors is defined by Sec 109.13. The prime contractor shall coordinate with subcontractors to assure all subcontractors are paid within 15 days. | |||
The Resident Engineer should provide the following to facilitate the process: The RE will provide an approved payment estimate to the prime contractor within 3 business days of the end of each estimate period. This approved payment estimate will provide a summary of all quantities paid to the contractor in order to facilitate the payment to the subcontractors. | |||
Issues related to this subject can be forwarded to [http://sp/sites/cm/Pages/default.aspx Construction and Materials]. A related subject, Prompt Payment of Contractors, is related to [https://revisor.mo.gov/main/OneSection.aspx?section=34.057 RSMo Missouri Revised Statute 34.057]. | |||
==109.14 Price Adjustment for Fuel (for [http://www.modot.org/business/standards_and_specs/SpecbookEPG.pdf#page=4 Sec 109.14])== | |||
Prior to bid, the contractor must determine whether they will bid their project based on projected fuel prices, or if they will choose to utilize the fuel price adjustments provided in Sec 109.14. In their bid proposal, they will choose to accept or decline receiving a fuel adjustment for the bid items identified in Sec 109.14 when the contract is executed. Bidders must choose to accept or decline the fuel adjustments for qualifying pay items in each of the four categories: excavation (production), asphalt paving (production & hauling), concrete paving (production & hauling), aggregate base (hauling). Production factors account for fuel used in producing and placing a product (e.g. asphalt plant burner fuel, paver fuel, distributor fuel, etc.), whereas On-Road Hauling factors account for fuel used to haul the material to the project. The On-Road Hauling factor is based on a 30-mile round trip. This is an average factor that is always used regardless of the actual haul distance. | |||
AWP automatically calculates the fuel price adjustment for all known qualifying standard pay items. Per Sec 109.14, non-standard pay items (generally designated with a "99" item number) do not qualify for fuel adjustment unless there is a Job Special Provision that overrides the spec and states the fuel adjustment shall apply to that item. Each estimate should be checked to verify that the appropriate fuel adjustments are being made either manually or auto-generated. | |||
{|style="padding: 0.3em; margin-left:7px; border:2px solid #a9a9a9; text-align:center; font-size: 95%; background:#f5f5f5" width="280px" align="right" | |||
|- | |||
|<center>'''[https://epg.modot.org/forms/CM/Fuel_Adjustment_Calculation.xlsx Fuel Adjustment Calculation Spreadsheet]'''</center> | |||
|} | |||
A [https://epg.modot.org/forms/CM/Fuel_Adjustment_Calculation.xlsx Fuel Adjustment Calculation spreadsheet] is available for manual calculations. Prior to calculating the adjustment, a check must be done to verify that the unit pay item matches the unit shown in the table in Sec 109.14. If not, a quantity conversion must be done before calculating the adjustment. For example, asphalt paid by the square yard would need to be converted to tons before multiplying by the corresponding factors in the table. The manually calculated fuel adjustment should then be added to the estimate as a [[:Category:101 Standard Forms#AWP CO Item Adjustments|CO Item Adjustments]] for the designated lines. The spreadsheet calculations should be retained in eProjects as documentation. | |||
Payment for work should be made in the pay period (or at least a pay period in the same month) in which the work was performed in order for AWP to calculate the fuel adjustment accurately. If payment for work is submitted via AWP in a time period other than the month in which the work was performed, a manual fuel adjustment will be necessary. When this happens, the fuel price adjustment must be calculated for the correct estimate period and a contract adjustment must be made to correct for the difference in the index for the two estimate periods. Calculations should be retained with the contract documentation. | |||
A table listing the Monthly Fuel Indexes is available in the right column under "Documents" on [https://www.modot.org/bid-opening-info MoDOT’s Contractor Resources website]. | |||
<div id="The following table provides"></div> | |||
The following table provides further guidance on when the fuel adjustment is applicable: | |||
<center> | |||
{| border="1" class="wikitable" style="margin: 1em auto 1em auto" style="text-align:left" | |||
|+ | |||
! style="background:#BEBEBE" align="center"|Pay Item!! style="background:#BEBEBE" width=450px align="center"|Does Fuel Adjustment Apply? | |||
|- | |||
|Asphalt pavement, shoulders, and entrances (full depth and overlays)||width=400px|Yes, all asphalt in [http://www.modot.org/business/standards_and_specs/SpecbookEPG.pdf#page=7 Sections 401], [http://www.modot.org/business/standards_and_specs/SpecbookEPG.pdf#page=7 402], [http://www.modot.org/business/standards_and_specs/SpecbookEPG.pdf#page=7 403] and ultrathin bonded asphalt wearing surface. | |||
|- | |||
|Job Order contracts ||width=400px|Fixed-cost pay items in Job Order Contracts do not qualify because they are considered “repair” work and not “construction” work. This exclusion is stated in Sec 109.14. | |||
|- | |||
|Concrete pavement (including pavement overlays), concrete base, shoulders, and entrances (i.e. 7” or 8” Paved Approach)||width=400px|Yes. For overlays that have separate pay items for placing (SY) and furnishing (CY), only the square yards of placing should receive a fuel adjustment. For overlays that are paid entirely in CY, the unit of measure should be converted to SY and the adjustment should be paid based on SY at the theoretical thickness. | |||
|- | |||
|Concrete Bridge Approach Slab and Concrete Approach Pavement||width=400px| No | |||
|- | |||
|Roller compacted concrete||width=400px| Yes | |||
|- | |||
|Concrete sidewalk, median strip (concrete or asphalt), or curb & gutter|| width=400px|No | |||
|- | |||
|Full or partial depth pavement repair, asphalt and concrete||width=400px|No, this concrete or asphalt material is for “repair”, not “construction”. Nor would the base rock for pavement repair. | |||
|- | |||
|Concrete or asphalt bridge deck overlays|| width=400px|Deck overlays do not qualify except when the roadway asphalt overlay extends across the bridge deck. | |||
|- | |||
|Seal coat, micro-surfacing, etc.|| No | |||
|- | |||
|Stabilized Permeable Base || Yes | |||
|- | |||
|Type A2 and A3 shoulders (concrete and asphalt) ||width=400px|Yes, both the surface material and the base rock qualify, but not the portion of base rock identified as incidental. | |||
|- | |||
|Aggregate surfacing||width=400px| No, aggregate under [http://www.modot.org/business/standards_and_specs/SpecbookEPG.pdf#page=6 Section 310] does not qualify. | |||
|- | |||
|Other base rock such as 12" or 18" Rock Base (Section 303)||width=400px|No. Only Type 1, 5, 7, and Stabilized Permeable Base qualify. | |||
|- | |||
|Base produced from rock on the project or from an adjacent source||width=400px| No, the material must be hauled to the project. | |||
|- | |||
|Non-standard bid items. These are items not specifically listed in the Listing of Bid Items For Highway Construction at the time of letting (i.e. item numbers with a “99” designation).||width=400px|No, not unless there is a JSP that specifically overrides Sec 109.14 and allows a fuel adjustment. | |||
|} | |||
</center> | |||
==109.15 Price Adjustment for Asphalt Cement== | |||
See [[:Category:403 Asphaltic Concrete Pavement|EPG 403 Asphaltic Concrete Pavement]] for guidance on AC price index adjustments. |
Revision as of 13:37, 19 November 2024
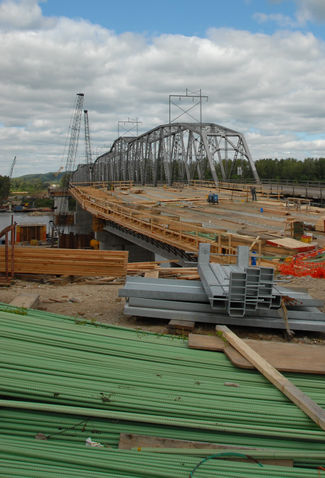
This article provides additional guidance related to measurement and payment, as defined in Sec 109, and sets forth uniform and effective procedures for the maintenance of records necessary to document project payments. Documentation procedures shown are considered to be the minimum required to authorize payment for an item. It is not intended to discourage other or more detailed documentation should either or these be appropriate to the situation.
It is intended that detailed records be prepared for all items and especially for those not accessible when a project is complete or for any pay item that does not remain a part of a completed project.
The specifications provide the basis of payment and a description of most items. Field measurement, final plans and remarks instructions are included in this article for that specification or may be obtained from the Constructions and Materials division.
EPG articles are not referenced as "sections" but as EPG XXX.X to avoid confusion with MoDOT specs (which are contractually binding). |
109.1 Measurement of Quantities (for Sec 109.1)
Force Account Spreadsheet |
Force Account Worksheet example |
Change Order Reports |
Change Order Overview |
Order Codes |
Change Order Time Extension |
Change Order Value Engineering |
Change Order, No Cost Contract Modification |
[1] |
Contract Adjustments |
Contractor Pay Estimates |
Line Item Adjustments |
Stockpiled Materials |
Measurements performed, and the associated calculations, should be well documented in the project records and should be recorded to no less than the minimum specified precision of the measurement. (For example: “Measurement will be made to the nearest linear foot” means to measure to no less than the nearest linear foot.) Confirm that the tools being used to make the measurement are accurate within the range required for the measurement. Calculations may be made manually, with a calculator or a computer but in each instance the results should be independently verified to eliminate math, keystroke or computer related errors.
Specifications typically have a "Method of Measurement" clause that indicates the minimum unit of measurement and pay. Each day that a work item is reported, the total quantity of work completed or material placed that day is to be totaled and then reported to a degree of accuracy no less than what is designated in the specification. Rounding is generally not necessary. For instance, tickets for hot mix asphalt generally show the measured quantity to the nearest hundredth of a ton even though the degree of accuracy per spec is only required to be to the nearest tenth of a ton. The tickets should be totaled to the nearest hundredth and reported to that accuracy in AWP each day. The daily quantity does not need to be rounded nor does the final pay quantity at project closeout need to be rounded.
When payment is made per station, it should be assumed that the work is performed in a single pass through the project limits and that the work may be along the centerline, on either side or on both sides. For example, work on both sides of the centerline that is one station long is to be paid as one station of work, not two. This guidance is to be waived when the specifications or plans are explicitly contradictory.
109.2 Scope of Payment (for Sec 109.2)
Payment to the contractor and the exceptional situations that may affect payment are covered by Sec 109.
109.3 Compensation for Altered Quantities (for Sec 109.3)
Typically this applies to Major Items, which are marked in the Items window of AWP. When there are no major items identified on the job, the greatest cost items on the job, that aggregately add up to 60% of the contract, are defined as the major items even though any one of them does not meet the 10% criteria of a Major Item.
109.4 Differing Site Conditions and Changes in the Work (for Sec 109.4)
Differing site conditions include subsurface or latent physical conditions at the site differing materially from those indicated in the contract, or unknown physical conditions of an unusual nature differing materially from those ordinarily encountered and generally recognized as inherent in the work. Changes in, or extra, work includes items of work not provided for in the contract as awarded, but found essential to the satisfactory completion of the contract.
109.5 Force Account (for Sec 109.5)
When it is impossible to reach agreement on a fair price for necessary extra work having no unit bid prices, the work must be done on a force account basis. This means that the contractor will be reimbursed for the actual cost of labor, insurance and tax, equipment and materials. In addition, the prime contractor will receive specified percentages of these costs to cover supervision, overhead and profit. Contract provisions for this method of settlement are set out in Sec 109.5. Per the specification, the prime contractor will receive an amount equal to five percent of the actual cost of subcontracted work. Actual cost is defined as including the subcontractor’s work, overhead and profit.
Before work is done on a force account basis, a change order must be approved to provide funds and authority for the work. The change order must be supported by the best available estimate of cost. The estimate should be carefully prepared to prevent large variations of actual cost from the estimate. Reference EPG 109.12.1.3 for more information on how to set up the pay item for Force Account work.
Daily records must be kept during progress of the work. This avoids later misunderstanding about the cost. Keep these records on the Force Account Spreadsheet of the Force Account Worksheet. An example of the force account worksheet is available.
109.5.1 Daily Force Account Record, Labor Account
Use the Force Account Spreadsheet of the Daily Force Account Record, Labor Account, as follows:
- In the upper right corner, place the number of the change order that originally authorized the force account work. This will serve to identity all associated reports. If the work is temporary erosion control authorized by order record, use the order record number and initials, O.R.
- Number the report consecutively for each day's work until the operation is completed. Write “Final” after the report number on the last daily report.
- Route, county, and project should be placed in the appropriate spaces.
- Give a fairly detailed description in the space provided for Description of Work. Include the location of the work to be done. Place this data on Report No. 1. It need not be repeated on subsequent daily reports.
- (a) The people employed on the work must be listed daily. This makes it necessary for the contractor to furnish the required information for each employee expected to be used on the work. Separate lines are provided for regular and overtime hours. The hours shown for each employee should be the actual hours worked each day. Separate columns are provided for the rate per hour and the fringe benefit rates per hour. The rates shown should be verified by a copy of the contractor's payroll, if available, or from the contractor's statement required by Sec 109.5.7.
- (b) Lead workers, as described under Sec. 109.5.1, must be paid no less than the prevailing hourly wage for the classification they are working in. If a lead worker is salaried, the contractor must provide documentation of the amount actually paid and the hours actually worked. This documentation is required by Sec 109.5.7. Salaried superintendents are not covered by the prevailing wage provisions and should not be included in the labor account. Their expenses are covered by the 20 percent overhead and profit as provided in Sec 109.5.2.
- If actual wage rates and fringe benefits cannot be determined in advance, it will be satisfactory to use rates shown in the contract for each classification. If rates from the contract are used, it will be necessary to obtain the actual rates paid by the contractor and make revised sheets before preparing the Force Account Spreadsheet of the Summary of Costs for the force account work. The contractor’s representatives should sign any revised sheets.
- Total the labor account at the end of each day. Add the previous day's total to get a running total to date.
- Check the appropriate spaces at the bottom of the page to indicate whether there were any materials or equipment charges that day. If the answer in both cases is no, the "Equipment and Materials Account" will not be required for that date.
- On the lower left of the form is space for the signature of the resident engineer, or of the employee designated in writing to sign the daily forms. ALternately, this can be done by attaching a digital signature to the form once it has been changed to a pdf document.
- The employee designated in writing by the contractor shall sign immediately below MoDOT's representative. Insert the name of the contractor below the space for this signature.
- Give the contractor the original and retain two copies. The MoDOT copy may be retained electronically.
109.5.2 Daily Force Account Record, Equipment and Materials Account
Complete this portion of the Force Account Spreadsheet of the Worksheet, if either materials or equipment charges were assessed for the day. Place the same information in the upper right corner as was placed on the Labor Account portion of the Worksheet. The report number is to be consecutive for the Equipment and Materials Form. It need not agree with the number on the Labor Account Form.
The headings for the various spaces under Materials Account are self-explanatory.
Each equipment unit must be listed separately. The contractor must supply information on all equipment to be used on a force account basis. The information must be in sufficient detail to allow accurate determination of the allowable rental rent according to Sec 109.5.4.
Rental rates on file with the Commission are the rates contained in Rental Rate Blue Book for construction equipment. Equipment Rental Rates from the Blue Book For contractor-owned equipment, apply the Model Year and Region adjustments, then divide the monthly rate by 176 hours to obtain the FHWA approved hourly rate. The listed estimated operating cost per hour is also applied for the time the machine is in use.
In all other cases, the resident engineer should negotiate rental rates with the contractor, subject to approval by the district. Sec. 109.5.4 states, "In no case shall the rental rates exceed those of established distributors or equipment rental agencies.” Proposed rates for contractor owned equipment may not exceed the rate determined by the above paragraph or the rate charged locally by equipment rental companies, whichever is lower. If special cases indicate that higher rates may be justified, send the proposed rates to Construction & Materials with the district's recommendation and data to support the proposed rates for division review.
Contractor's proposed rates shall be submitted to the resident engineer in writing. The proposal shall state whether the rate includes fuel and lubricants. After district concurrence, the resident engineer shall grant approval in writing. The written proposal and approval make up the agreement. Send both letters to the district with the Force Account Spreadsheet of the Daily Force Account Record, Summary of Costs after the work is done.
When this has been done, use of the various column headings is based on the agreement. The columns for No. Hours, Previous Hours, and Net Hours are self-explanatory. They are to be used regardless of rental basis.
If equipment is to be used on an hourly rental basis, the Hour Rate multiplied by the Rate Adjustment Factor will be used. In all other cases, list the rental on either a weekly or monthly basis as agreed.
When equipment is rented from a recognized rental agency specifically for the force account work, the contractor will normally be allowed the actual rental paid. This must be established by paid invoices.
If contractor-owned equipment must be kept available full time at the site, or if it is specialized equipment for which there is no other use on the project, it may become necessary to allow rental on a full time basis. The unit should then be shown at 8 hours of rental for each day, Monday through Friday, at the hourly rate established as outlined in the Rental rates on file with the Commission paragraph, above, unless the resident engineer has authorized overtime use of the equipment. If the agreed rate is "bare" rate, the agreed operating cost per hour would be added to the "bare" rate only for actual operating hours.
If contractor-owned equipment is to be used on a part-time basis and will be used for other work on the project, it should be carried on the equipment account at actual hours used.
If equipment must be shipped to the project specifically for force account work, the shipping costs are reimbursable. Such costs should be carried in the equipment account by listing the unit involved and showing the shipping cost under amount. Write in the invoice number, noting it as shipping cost, under the rate headings.
For the time required to move the equipment to and from the site of the ex work and any authorized standby time, the rate will be 50% of the hourly rate after the actual operating costs have been deducted.
109.5.3 Force Account Record, Summary of Costs
The Summary of Costs, Force Account Spreadsheet, is prepared in quadruplicate when the force account work has been completed.
On the Summary, place in the upper right corner the number of the original authorizing change order. Complete the description and location of work in considerable detail.
Give the original to the contractor. Retain the fourth copy in the resident engineer's file. Send the other two copies to the district office for checking.
One copy sent to the district office is to be accompanied by a copy of each daily report for checking. The daily reports, after checking, are to be filed with the district copy of the Force Account Record Summary of Costs.
109.6 Method of Payment (for Sec 109.6)
Contractor payments are made electronically to the contractor’s designated financial institution on the basis of the payment estimate which is created twice a month when work on a contract is active.
Payment estimates must be supported by documentary evidence that work items allowed have actually been done. Evidence may be in the form of scale tickets, diary entries, material receipts, etc. The payment estimate is intended to provide payment to the contractor for all work performed during the estimate period. In no case should payment for work be delayed beyond the estimate period following the period in which the work was performed.
Earthwork quantities may, for example, be supported by load count entries in the inspector's diary. Another way is by diary entries giving limiting stations of completed balances.
Weight or volume tickets are a sound basis for allowing payment on items measured in this manner.
Check all items against inspection records to be sure they are properly approved.
- Provide equitable payment. If work remains to be done (for example, patching the tie holes in concrete) allowance for the appropriate pay item should be reduced. The reduction should be the amount estimated as the cost of completing the work. Make allowance in full for all completed items.
- Items to be paid for by Planning in connection with weight station complexes are to be included on the regular Engineer's Payment Estimate. At conclusion of this work, a certification is to be submitted with the estimate stating that the scales and material used met specification requirements.
- Bid items not covered in the bid item master list will be indicated in the description block by the term "Miscellaneous" and supplemental number. The resident engineer may insert an abbreviated description using AWP.
- Engineer's Payment Estimates should be submitted for liquidated damages even when no pay items are listed. Such estimates indicate a negative amount due the contractor; accordingly, no payment can be made and no further action is taken.
109.7 Partial Payments (for Sec 109.7)
Partial payments are payments made over the course of the contract each estimate period, and payments made for material allowance.
109.7.1 Payment Estimates
Payment estimates are generated by the AWP computer software application.
109.7.1.1. Estimates will be generated for all active contracts, regardless of the amount of payment encountered during the estimate period. This includes all estimates for contracts which will produce payment, "no pay" estimates (zero dollar value) and estimates which result in a negative payment.
Should the contract be inactive and a series of estimates will be no pay estimates, a letter or e-mail shall be sent to the contractor with a copy to the controller's office stating estimates will not be generated during the following time periods because there is no work conducted on the contract. The controller's office will record this information and will not contact the Resident Engineer because estimates haven't been generated for a specific time period.
109.7.1.2. The first level of estimate generation will be designated by the Resident Engineer at the time of contract activation. The Resident Engineer will notify the AWP Administrator who this person shall be. This person must have project manager access to the system.
Progress estimates will be generated for estimate end dates of, generally, the 1st and 15th of each month. The controller's office will issue a chart of estimate due dates annually. AWP estimates must be approved by Level 2 (Resident Engineer) no later than 4:00 PM on the day listed on the chart as "Due in Controller's Office."
109.7.1.3. Estimates may be generated repeatedly prior to the estimate ending date, in order to resolve discrepancies or check quantities. Two payment estimates shall be made per month for active contracts. The official pay estimates shall be generated with the period ending dates of the 1st and the 15th, making the estimate periods typically the 2nd day of the month to the 15th day, and the 16th day to the 1st of the following month. There may be exceptions to the estimate periods depending upon the financial systems such as the end of the state fiscal year. Other exceptions may be made to the estimate period depending on the status of the contract or as notified otherwise by the AWP Administrator and in the first paragraph of EPG 109.7.1.4, below.
All indexes based upon a monthly index value shall use the same index value for the entire estimate period even though the index value may be reestablished on the 1st of the month. For example the asphalt and fuel index values change on the 1st of the month, but any work completed on the 1st shall use the same index value as the previous month so that the entire 16th to 1st estimate period uses the same index value.
Estimates can be re-generated without deleting the existing estimate from the Estimate History window. Do not use the "delete" option to delete an estimate. To re-generate an estimate for a pay period, just generate that estimate. The system will indicate that an estimate already exists for the period, and will prompt “Would you like to delete?” (meaning to overwrite the existing estimate.) Select "Yes", which will reset the tables and the estimate will be generated containing any new information that has been added.
109.7.1.4. The progress estimate for the period ending July 1 of each year shall be changed by the user to the period ending date of June 30th, prior to estimate generation. This change shall be made to coincide with the MoDOT Fiscal Year End cycle.
Supplemental estimates will not be generated unless specifically instructed to do so by the AWP administrator.
Final Estimates shall be generated by the Resident Engineer prior to submission of the final plans to the District for checking. When logged into the system as a Resident Engineer, only final estimates can be generated. For a Resident Engineer to generate a progress estimate, they must log in as a project manager.
109.7.1.5. Payment estimates must be supported by documentary evidence that work items allowed have actually been done. Evidence may be in the form of scale tickets, diary entries, material receipts, etc. Earthwork quantities may, for example, be supported by load count entries in the inspector's remarks. Another way is by remarks entries giving limiting stations of completed balances. Weight or volume tickets are a sound basis for allowing payment on items measured in this manner. The payment estimate is intended to provide payment to the contractor for all work performed during the estimate period. In no case should payment for specification compliant and accepted work be delayed beyond the estimate period following the period in which the work was performed.
Check all items against inspection records to be sure they are properly approved.
109.7.1.6. The Division Final Plans Reviewer shall notify the Resident Engineer when the final estimate is approved and the final plans are passed for payment. Once the Resident Engineer receives the notification, the Resident Engineer will send the prime contractor the Estimate Summary Report(s) for the final estimate as outlined below:
- General: The Cognos report “Estimate Summary for Contract, By Estimate Number” is the official estimate report to send to the prime contractor on all MoDOT contracts administered through AWP. This will establish the policy and procedure related to this function of AWP.
- Prior to producing this report, it shall be the responsibility of the Resident Engineer to verify the accuracy of the estimate and to approve the estimate in AWP. The Resident Engineer will make this verification by confirming the Last Approver ID is the User ID of the Resident Engineer in the Estimate Summary of each contract.
- After the RE has verified the estimate has been approved at the Resident Engineer level, the Estimate Summary for Contract, By Estimate Number shall be electronically saved as a .pdf file in eProjects. Refer to EPG 137 Construction Inspection Guidance for Records to be Maintained for more information on saving reports produced from AWP or information retrieved from AWP.
109.7.2 Material Allowance
Under stockpile materials should appear those items for which a payment may be made in accordance with the general requirements. Check the specification for the minimum acceptable material allowance. Non-perishable items to be incorporated in the finished product may, in general, be included on the estimate for stockpile materials provided satisfactory inspection reports, certifications or mill test reports and required invoices are in the project file. When the item first appears on the estimate, the resident engineer must have on file a copy of an invoice to substantiate the unit prices allowed. Receipted bills for all materials allowed on the estimate must be furnished to the resident engineer within the time established by specifications, or the item must be eliminated from future estimates. Missouri state sales tax may be included in material allowances if shown on invoices or receipted bills. Each receipted bill must be marked or stamped paid with date of payment shown, as well as the name of the firm and signature of the person who received payment. All invoices and receipted bills obtained to substantiate material allowances during progress of the project are to be filed in the district as part of the permanent project record.
Some aggregates are accepted for "quality only" at the point of production. Total acceptance is not made at the time of production because additional processing and/or screening are required before incorporation into the final product. If gradation tests, which are run for information purposes only, indicated it is reasonably possible to produce an acceptable finished product, this material may be included in the stockpile material payment.
If test reports or visual inspection on the above material or other material that might be produced and accepted indicate that it will be unsatisfactory at a later date due to gradation, excess P.I., segregation, contamination, etc., these materials should not be included on the stockpile materials payment.
The price per unit for material produced by the contractor or by a producer other than an established commercial producer should reflect the actual cost of production. The units shown under material estimate should be the same unit of measure used in the bid item where possible, such as pound for steel, linear foot for piles, etc. Where this is not possible, a convenient unit such as ton for aggregate should be used. Quantities in excess of contract requirements should not be allowed. Hauling costs should not normally be included in the unit cost of any material unless it has been hauled to a site where it can immediately be incorporated in the finished product or work. If hauling cost is allowed, it must be considered with relation to the value of the material in case it is necessary for the state to take it over. Stockpiling costs are not to be included as part of the unit cost.
Items that are to be accepted by project personnel must be inspected and found satisfactory prior to being included on a stockpile materials payment. Quantities for materials included on a stockpile materials payment should never exceed approved quantities.
Before an allowance will be approved for payment on material stockpiled or stored on private property, or for aggregates stored on property operated as a commercial business, a lease agreement from the contractor or subcontractor showing compliance with the following points must be submitted to the district office for approval.
- 1. A complete land description covered in the lease form and the haul distance from the lease area to the project.
- 2. The following statement included in the lease agreement:
- "It is understood and agreed by the parties hereto that the land herein involved is to be used as a materials storage site and that the prime contractor, whether or not the lessee herein, may obtain payment from the Missouri Highway and Transportation Commission for material stored thereon".
- "It is further understood and agreed by the parties hereto that the prime contractor or contractor having a written agreement with the Missouri Highway and Transportation Commission for the construction of highway work involving this lease and the materials stored thereon, whether or not the lessee, and the employees of the Missouri Highway and Transportation Commission shall have the right of access to the property covered by this lease at all times during its existence and that in the event of default on the part of the lessee or the prime contractor, if other than lessee, the Missouri Highway and Transportation Commission may enter upon the property and remove said materials to the extent to which advance payments were made thereon".
- An area leased on property operated as a commercial business must be posted so as to divorce the site for stockpiling of highway materials from the commercial operation.
- If either party to the lease agreement is incorporated, it is essential that an Acknowledgment by Corporation be attached for each corporation involved since an individual cannot legally bind a corporation without duly enacted authorization by the corporation's Board of Directors. A suitable form for this purpose is shown in Agreement for Shifting State Highway Entrance, page 1. Other forms may be used by some corporations and are acceptable if they fulfill the intent of the form illustrated. Leases involving corporations should not be accepted without the Acknowledgment.
- Signatures by individuals must be notarized, or be witnessed by at least two disinterested persons. The address of witnesses should be shown.
- When material is stored on property owned by a railroad and is accessible by a public roadway, it is not necessary to obtain a lease agreement to permit this material to be placed on the estimate as a stockpile material.
- If hauling charges are to be included as part of the cost of materials allowed for payment, invoices for hauling charges must be provided by the contractor in the same manner as invoices for the material. An exception to this requirement is allowance for the cost of the rail freight. For rail freight the contractor should supply a copy of the first freight bill to substantiate the freight rate. In lieu of submitting receipted freight bills, the contractor may then sign a statement on each material invoice indicating that freight charges have been paid. If the contractor prefers, a letter may be submitted listing several invoices and indicating freight charges that have been paid. Whichever procedure is adopted, the resident engineer must be assured that freight charges have been indicated as paid for all materials invoices submitted to verify quantities.
- The engineer may also include in any payment estimate an amount not to exceed 90 percent of the invoice value of any inspected and accepted fabricated structural steel items, structural precast concrete items, permanent highway signs, and structural aluminum sign trusses. These items must be finally incorporated in the completed work and be in conformity with the plans and specifications for the contract. These items may be stored elsewhere in an acceptable manner provided approved shop drawings have been furnished covering these items and also provided the value of these items is not less than $25,000 for each storage location for each project.
- The engineer may also include in any payment estimate, on contracts containing 100 tons or more of structural steel, an amount not to exceed 100 percent of the receipted mill invoice value of structural carbon steel or structural low alloy steel, or both, which is to form a part of the completed work and which has been produced and delivered by the steel mill to the fabricator.
While the nature and quality of material is the contractor’s responsibility until incorporated into the project, material presented for stockpile materials payment must be inspected prior to being approved for payment. The nature of that inspection is at the discretion of the engineer and may include sampling and testing to determine whether the material has a reasonable potential of compliance, once incorporated into the project. This sampling and testing may occur wherever the material is offered for stockpile materials payment, including stockpiles in quarries and at other off-project sites. Material that is a component of a mix may be compared to the associated mix design or to any other specification criteria that may apply.
109.8 Final Acceptance and Payment (for Sec 109.8)
In addition to confirmation of final quantities, all other adjustments to the contract amount should be reviewed and verified prior to making final payment to the contractor. See EPG 105.15.2 for guidance on the Final Acceptance process.
Contractor's Affidavit Regarding Settlement of Claims (C-242)
Contractor's Affidavit Regarding Settlement of Claims (C-242) with Exceptions
Addressing claims from creditors (e.g. supplier, sub, etc.) against the prime contractor:
Intervening in pay disputes between the prime and their creditors should be limited to facilitation efforts by the RE. The RE should contact the prime, discuss details of the payment issue, and advise of Missouri’s Prompt Payment Law if there is not a valid reason for their delay in payment. If no resolution can be facilitated, provide the creditor with the Surety’s name and contact information, as listed in the contract bond. Also, note the name and nature of the dispute for a reference when the C-242 is received at the completion of the job. Pay retainage should not be withheld from the estimate because of a creditor claim. Payments should not be made to the Surety unless the contract is declared to be in default and the Surety submits a formal letter requesting all future contractor payments go directly to them. If the dispute is not resolved prior to the Final Inspection, provide the contractor with the Contractor's Affidavit Regarding Settlement of Claims (C-242) with Exceptions form so that they can list all pay disputes and state the reason why full payment was not made. Contact the Division of Construction and request authorization to close out the job despite the unsettled claim(s). Projects will typically be authorized for closure unless the dispute is deemed to directly involve the Commission. If the pay dispute involves a Disadvantaged Business Enterprise (DBE), advise External Civil Rights of the details surrounding the dispute.
109.9 Retained Percentage (for Sec 109.9)
Formal retainage is no longer designated by MoDOT as a routine part of the contract however 34.057 RSMo does allow up to 10% of the contract price to be retained in order to ensure performance of the contract. Payment may be withheld on any particular work item that has not been completed in accordance with the contract. This can include work incidental to the work item, and required documentation directly related to the work.
109.10 Contract Assignment Process - Contract Reassignment to a New Contractor (for Sec 109.10)
The Missouri Highway and Transportation Commission (MHTC) and MoDOT advertise construction projects, open bids and award several hundred contracts each year. Typically, the awarded contractor performs the work, with subcontractors, through completion and the contract is closed out. Sometimes contractors may be purchased by other contractors, may have taken on too much work, or decide for other reasons not to finish a contract they were awarded, and then wish to make an arrangement with another contractor to complete the project(s) under the same contract conditions. MoDOT has prepared for this slight possibility with a process for transferring the contract to a new prime contractor by reassigning the contract through an “Assignment Agreement”, subject to consent and approval by the MHTC. Chief Counsel's Office has created template assignment agreements for the typical scenarios. The Construction and Materials Division is responsible for working with the contractors to process the assignment agreement allowing the new contractor to work on the project and collect payment from MoDOT.
Although the original contract remains in place, the assignment agreement assigns responsibilities for completing the contract to the new contractor. MoDOT does not pay any additional compensation to the contractor when agreeing to an assignment, nor does either contractor pay MoDOT any compensation for the transfer. The original contractor (assignor) and the new contractor (assignee) have their own agreement regarding this transaction which sometimes includes transferring other assets from one contractor to the other. MoDOT is only concerned with continuing surety protection while the work is still active and completing the contract on time and within budget. MoDOT and the MHTC could object to a transfer, but the likely outcome is a situation where the original prime contractor has been purchased, has no assets remaining and their surety would have to be engaged to complete the work. Therefore, consenting to the assignment is generally in the best interest of all involved parties and likely the best way to get work completed in these situations.
Once a contract is reassigned, the new contractor (assignee) is the responsible contractor that MoDOT expects to and is contractually obligated to complete the work, will be paid for work completed and will be held accountable to finish the contract on time and within budget. MoDOT will change the information in the contract administration system to recognize the new contractor and the Resident Engineer’s office will be notified of the changes. See the Assignment Matrix for the details of the reassignment process.
109.11 Compensation for Project Delays (for Sec 109.11)
Sec 109.11 designates the conditions for which compensation may be appropriate to cover the cost of a project delay. Review the specification and refer any questions to the Construction and Materials Division.
109.11.1 Documentation of Delay Costs
When a delay has been determined to be compensable (that is, it was directly caused by the Commission), and the contractor has claimed impact costs due to the delay, reference Sec 109.11.1 for a list of eligible delay costs. An additional 10% is added to the sum of these costs to account for home office overhead and all other costs. The total of all costs, plus the 10% mark-up, should be summarized on a Documentation Record as supporting documentation for the lump sum delay cost change order. The Force Account spreadsheet should not be used as those accounting methods are only for added work and include other mark-up rates for profit and overhead.
There are four categories for additional costs. Below further clarifies what is included in each of these items.
- (a) Non-Salaried labor expenses. This is most commonly for trade workers who are compensated on an hourly rate. This would be for workers such as laborers, carpenters, iron workers etc. During a delay there may be activities that need to still be ongoing. This would include activities such as traffic control and erosion control. Salaried workers are non-compensable. These workers can be reassigned to other projects or perform other activities. Their salary is ongoing and would be incurred regardless of the delay. Labor rate increases are allowed. For example, paving was to be performed in October and due to the delay, it could not be performed until May. A labor rate increase went into effect in January. Therefore, the net labor increase for the hours worked on the paving would be allowed. This does not apply to increases in prevailing wage rates as the original wage order remains in effect for the life of the project. The only mark-up for labor costs, prior to the 10% overall markup, should be inclusion of additives for insurance and taxes (FICA/FUTA/SUTA/General Liability/Work Comp).
- (b) Material costs. This is for an increase in costs for materials due to the delay. Actual documented increases in costs for materials due to the delay is allowable. For example, a bridge deck scheduled to be poured in October is now being poured in March due to the delay. The concrete price was increased in January. Therefore, the net increase in concrete material cost is allowed.
- (c) Equipment costs. This is the cost of on-site equipment that is idled. It would not include trucks or other mobile equipment that can readily be relocated. The reimbursement method is outlined in detail in Sec 109.11.2.
- (d) Costs of extended job-site overhead. These are ongoing costs such as the job site office, porta-potty rental, utilities, dumpster rental etc. that are extended due to the delay. (It does not include cell phone costs which are portable and not tied to the project.) These costs are only compensated for the period from the original completion date to the extended completion date as a result of the delay. This applies even if the contractor’s submitted schedule indicates they would have completed the project before the original completion date (since there is no guarantee that the project would have been completed ahead of the original completion date).
109.11.2 Calculation of Equipment Delays
Equipment costs should be limited to on-site equipment that remains inactive due to the compensable delay. In lieu of computing actual ownership cost of the equipment, the Non-Active Use Standby Rate, as published in EquipmentWatch, shall be used to calculate the costs of idle equipment owned by the contractor. Multiply the hourly standby rate by 8 hours for each full weekday/non-holiday elapsed during the delay. If the delay extends for a month or more, use 176 hours/month. For rented equipment, payment will be made per the actual rate in the rental agreement.
Long-Term Delays
If the delay is anticipated to be long-term, such that the projected delay cost would exceed the cost to mobilize the equipment from/to the job site, the Resident Engineer should inform the contractor in writing that they have the option to mobilize the equipment off-site for use elsewhere. State the earliest possible date resumption of work is anticipated. Clarify that payment for equipment standby costs will be made only from the start of the delay period through the date of the notice of the long-term delay. If the contractor chooses to mobilize the equipment off-site, actual mobilization costs from/to the site will also be paid. If the contractor chooses to leave the equipment on-site, no standby costs for equipment will be paid past the date of the Resident Engineer's notice.
109.11.3 Common Claims
No other overhead costs are reimbursable. See Sec 109.11.3 for a list of common claims that are contractually ineligible.
109.12 Change Orders
The primary purpose of a change order is to document a supplemental change to the contract. The official definition, as stated in Sec 101, is as follows:
- Change Order - A written order from the engineer to the contractor, as authorized by the contract, directing changes in the work as made necessary or desirable by unforeseen conditions or events discovered or occurring during the progress of the work.
The second most primary purpose of the change order process is to ensure proper authority has been granted before proceeding with revisions in quantities or changes in scope of work, design concept, time or specifications. Changes in scope should be limited to the original intent, purpose and limits (length and width) of the job. In instances where proposed changes in scope go beyond these original job parameters, the change order shall be considered a major change order (Sequence 4). Significant scope changes require the State Construction and Materials Engineer to discuss the requested changes with the Asst. Chief Engineer prior to granting approval.
Change orders must have approval at all required levels before the work proceeds. Exceptions are granted for routine or minor changes, or emergency revisions for which verbal approval has been granted. In rare cases it may be necessary to proceed with emergency measures without prior approval. In such cases, verbal approval should be sought as soon as practicable. Indicate in the DWR remarks the name of the individual who provided verbal approval. For change orders that provide payment for additional work, all attempts should be made to complete the process promptly so that the contractor can be compensated at the end of the pay period in which the work was performed.
Environmental Change Orders - Any design changes that include disturbance of new areas on the project, or that include any other unplanned environmental impacts, should be reviewed by the Project Manager to determine if a request for environmental services is necessary prior to implementation.
Job Order Contract Change Orders. Job Order Contracts have unique contract terms that limit spending to a budgeted amount and often include pre-approved time extensions. Reference EPG 147.3.9 Change Order Approvals for additional guidance on administration of change orders for Job Order Contracts.
109.12.1 Change Order Preparation
Change orders are generated in AWP, and subsequently displayed in pdf format using the appropriate Cognos change order form. Quick Reference Guides are provided below to provide details. All completed change orders and supporting documentation shall be in electronic format and stored in eProjects. Change orders shall be transmitted in the original electronic format and shall not be scanned. Ink-signed paper copies or scans from a contractor shall not be accepted. A QRG (Digital Signature for Adobe Reader DC or Pro DC) is available to assist contractors with creation of their digital ID, and registration of that ID with MoDOT. The contractor shall also inform the RE in writing who they authorize to approve change orders on their behalf.
Supplemental Documents. Supplemental contract documents that are pertinent to the change order directive, such as new or revised plan sheets, new or revised Job Special Provisions, revised cross-sections, etc., shall be merged with the change order form to create a single file in pdf format and saved to eProjects prior to sending to the contractor.
Supporting Documentation. Any pertinent supporting documents (e.g. Contingent Item Price Check form, relevant emails, letter of agreed price, computation sheets, mock Force Account computations, etc.) that provide additional details of the change, or provide justification of a price for contingent work, should be saved in eProjects as Supporting Documentation. All supporting documents should be merged into a single pdf document for each change order (the Force Account spreadsheets will require conversion to pdf format). At a minimum, any change order that contains a new contingent item should have supporting documentation that justifies the agreed price. More information on how to justify an agreed price can be found in EPG 109.12.1.3 Contingent Items - Settlement for Cost. Time adjustment change orders require supporting documentation (e.g. weighted time-table computation, analysis of how an excusable delay impacted the critical path, negotiated settlement narrative, etc.), unless the change order reason is self-explanatory.
Final Change Order. If a clean-up change order is necessary after project completion to adjust the quantity of one or more pay items to the final accepted amount, this is designated as the “Final” change order. If no final change order is necessary due to all quantities being updated to final status by previous change order(s), the contractor should be informed that records indicate no further quantity adjustments are needed and the project will be closed out, as is, with current quantities as listed on the most recent pay estimate.
The following Quick Reference Guides provide detailed information on how to create a change order in AASHTOWARE Project and how to create the contractual pdf form:
Adjust Mobilization for Contract Bond |
Chief Engineer Level |
Division Level |
RE Level |
Time Extension |
- AWP CO 2 Change Order Adding New Item or Overrun/Underrun of Existing Items
- AWP CO 3 Change Order Time Extension
- AWP CO 4 Change Order Value Engineering
- AWP CO 5 Change Order, No Cost Contract Modification
- AWP CO 6 Change Order, Mobilization and Contract Bond
- AWP CO 7 Change Order Approval
- AWP CO Change Order Codes
- AWP CO Change Order Reports.
109.12.1.1 Change Order Approval Level Criteria
This article provides the criteria to determine the required approval level of a change order. AWP assigns a sequence number to correspond with each approval level, as follows:
- Contractor level (Sequence 1) – Approval applied in AWP by the Construction Project Office Assistant.
- Non-major Change Orders:
- RE level (Sequence 2)
- District level (Sequence 3)
- Major Change Orders:
- Division level (Sequence 4)
- Chief Engineer/ Chief Financial Officer level (Sequence 5)
- FHWA Review (Sequence 6). If a project is designated for federal involvement for change orders on the PODI Matrix, and the change order is classified as district level or higher (i.e., Sequence 3, 4 or 5), review and approval by the Federal Highway Administration (Sequence 6) is required. RE level change orders do not require FHWA review.
The change order approval level criteria are listed below and available here in table form:
This chart is a graphic presentation of the criteria stated in EPG 109.12.1.1. All change orders require approval in AWP at Project Office Assistant role on behalf of the contractor (Sequence 1) AND the Resident Engineer role (Sequence 2). If the change order exceeds any of the criteria displayed in this chart, it would also need to be approved at the additional Sequence(s) shown. The chart values are absolute values. The criteria that requires the highest sequence approval always prevails over other criteria. |
Non-major change orders (Change Order Sequence 2) approved by the Resident Engineer are:
- 1. Any no-cost (zero dollar) change orders (used when the direct substitution of a particular line item with a contingent item does not generate an additional cost or cost reduction).
- 2. Any change in a contract or contingency item less than $50,000.
Non-major change orders (Change Order Sequence 3) that require approval from the district office, and by FHWA on projects designated for federal involvement on change orders on the PODI Matrix, are:
- 1. Any change in a contract item or contingency item from $50,000 to $100,000.
- 2. Any new contingency item from $50,000 to $100,000.
Major change orders (Change Order Sequence 4) that require approval from the division office, and by FHWA on projects designated for federal involvement on change orders on the PODI Matrix, are:
- 1. Any change in a contract or contingency item greater than $100,000.
- 2. Any new contingency item greater than $100,000.
- 3. Any specification change.
- 4. Any revision in a contract unit price.
- 5. Any change in a “Major Item” greater than 25% from the original contract amount for that line item (in dollars). A Major Item is defined in Sec 101 as, “having an original value in excess of 10% of the original contract amount.”
- 6. Any change of the contract amount greater than 25% of the original contract bid amount (also in dollars).
- 7. Any change in design concept.
- 8. Any change order not approved by the contractor.
- 9. Any change order for adjustments due to differing site conditions or significant changes in the character of the work.
- 10. All value engineering change orders regardless of cost.
- 11. Any change order granting a time extension.
Chief Engineer/Chief Financial Officer change orders (Change Order Sequence 5) meeting any of the three following criteria must have the concurrent approval of the Chief Engineer and the Chief Financial Officer, and FHWA approval for projects designated for federal involvement on change orders on the PODI Matrix:
- 1. Additions greater than 50% if the original contract amount was $500,000 or less.
- 2. Additions greater than 25% if the original contract amount was greater than $500,000.
- 3. Additions greater than $1,000,000.
109.12.1.2 Description and Reason for Change
The author of the change order should provide sufficient narrative to explain both the reason the change is needed and a description that clearly states any necessary contractual language to define the terms. Enough detail should be included to explain the circumstances to someone who may be unfamiliar with the issue, such as a reviewer or auditor. For contingent items, check to ensure controlling specifications are available that adequately define the work, including the method of measurement and basis of payment. Add any terms not covered by specifications or other contract language. For significant quantity changes, explain exactly what caused the overrun or underrun (e.g. grade change, incorrect shrinkage factor, error in Summary of Quantities, roadway width differed from typical section, additional asphalt needed due to excessive rutting, etc.). Slight quantity variations can be explained as “Final measured quantity, within normal tolerance".
109.12.1.3 Contingent Items - Settlement for Cost
When a MoDOT standard bid item exists for contingent work, use the item number and description from the Bid Items Listing. Miscellaneous “99” numbers are available in this listing for items that require a unique description.
If payment is to be made by force account settlement, use item number 109.4000 FORCE ACCOUNT, enter $1.00 for the unit price and set the quantity equivalent to the estimated cost. The quantity will be adjusted after the work is complete to reflect the actual cost, as determined by the force account summary.
A “Settlement for Cost” statement should be included in the Description and Reason for Change field for all new contingent items. Changes to contract pay items, or previously established contingent items, do not require this statement since the contract prices govern. The “Settlement for Cost” statement, when required, should refer to the basis of settlement (i.e., agreed unit price, a fixed price listed in Standard Specifications, or Force Account). The settlement statement should also state the unit price. Here are some examples of “Settlement for Cost” statements:
- “Settlement for cost of REPAIRING CONCRETE DECK (HALF-SOLING) shall be made at the agreed price of $69 per square foot.”
- “Settlement for cost of CLASS 2 EXCAVATION IN ROCK shall be made at $170 per cubic yard, as specified in Sec 109.16 Fixed Cost Items.”
- “Settlement for cost for FORCE ACCOUNT-MODIFY EXISTING DRAIN GRATES, as specified herein, shall be made per Sec 109.5 Force Account Computation.”
Justification of Agreed Price. Any contractor-proposed price for a contingent item shall be fully evaluated to ensure it is fair and reasonable before accepting it as the agreed price. Justification of the agreed price on any new contingent item shall be documented in eProjects as Supporting Documentation. Documentation is typically made on the Contingent Item Price Check form by comparing the agreed price to the Average Unit Bid Prices (BidTabs), or to a price for the same type of work on another area project. Sometimes documentation can be as simple as saving an email string that states the reason the price was deemed acceptable. For unique work for which no price comparison exists, or there are other factors that greatly affect the price, a detailed cost estimate (materials/equipment/labor) should be requested from the contractor that supports their proposal. If the RE concurs that the contractor’s breakdown of costs is reasonable, the price can be accepted. Another tool to arrive at an agreed price, especially for lump sum price quotes, is for project office staff to perform a mock Force Account analysis using anticipated materials, equipment and labor costs. If that total is reasonably close to the contractor’s proposal, the price can be accepted as an agreed price without invoking the force account process. If a price agreement cannot be reached, the RE should direct the contractor to proceed with the work under Force Account Computation per Sec 109.5.
All contingent work must be clearly defined (i.e., include a description of work, material requirements, construction requirements, method of measurement and basis of payment). References to the standard specifications may be used when available.
Settlement Clause (used only for settlement of a Claim or Controversy, as defined in Sec 101). When a change order involves a negotiated settlement and final resolution of a contentious issue, in order to clarify the settlement is all-inclusive for any associated claims for costs, the following language is recommended for insertion into the change order description:
- "The amount being paid to <Construction Company> in this Change Order represents a negotiated settlement and, as such, reflects payment of all claims of <Construction Company> and/or any of its subcontractors and suppliers direct and indirect, including all impacts starting from the date of execution of the contract until the execution by both parties of the Change Order. However, nothing in this Change Order affects <Construction Company>'s right to file a claim based on an occurrence after the date of this Change Order."
- Note: Delete the last sentence if the change order is being issued after all work on the project is complete.
109.12.2 Change Order Approval
Preview for Sequence 3, 4 or 5 Change Orders. All draft Major change orders shall be submitted to the to the Construction Liaison Engineer for initial review prior to submitting to the contractor. Likewise, all district level change orders shall be sent to the DCE prior to submitting to the contractor. This is only considered initial approval, change orders sent to the contractor should not contain any MoDOT approval signatures. MoDOT approval and signing shall occur after the contractor digitally signs the change order.
Following any required previews, the RE will submit the completed change order to the contractor as an attachment to an email. The contractor’s signature should be requested on all change order. If the contractor refuses to sign a change order, their refusal should be documented and disclosed to any subsequent approvers (i.e., district or division level approvers). If the decision is made to execute the change order without the contractor’s signature, all other approval signatures will be applied, and the executed change order will be sent back to the contractor as a directive to proceed with the change in work. If the unsigned change order includes new contingent item work, and no contract price or fixed price exists, payment for that portion of the work will need to be designated force account.
Once the digitally signed change order is returned from the contractor, the RE shall upload it to eProjects, sign, and then approve in AWP. For change orders that require district level or higher approval, the RE will then send an email to the District Construction Engineer with a direct link to the change order, along with a link to any supporting documentation. If the change order requires division level approval, the RE should also copy the Construction Liaison Engineer. After approval has been completed at the district level, the DCE will forward the email on to the Construction Liaison Engineer if division level approval is required. The highest-level approver will reply to the RE confirming that the pdf is signed and the change order is approved in AWP. For PODI projects that are designated for change order review by FHWA, the highest-level approver will forward the email on to the appropriate FHWA Transportation Engineer and copy the RE. The FHWA Transportation Engineer will reply to all when approved.
109.12.3 Time Adjustment Change Orders
All time adjustment change orders, whether for overall contract time, individual project time, or specified milestones (e.g. road/bridge closure), are considered major change orders and shall be reviewed and approved by the division office. Initial review by the Construction Liaison Engineer shall be made prior to any agreements with the contractor and prior to submitting the Time Adjustment change order to the contractor. Time adjustments are granted for events deemed by the engineer as excusable delays that inhibit progress of a controlling item of work (i.e., critical path schedule). Sec 108.14.1 lists some of the common events that warrant consideration. EPG 108.7 Contract Time for Completion of the Work provides guidance for determining the appropriate amount of a time extension. The AWP CO 3 Change Order Time Extension provides guidance on how to generate the time change in AWP. Justification for the extension should be documented and saved in eProjects as Supporting Documentation unless the change order reason is self-explanatory.
All time extension change orders should include a description and reason and for granting of additional time, the amount of days, and any terms associated with the extension. The description should identify the controlling item of work that was affected by the delay, as confirmed by examining the critical path schedule. If the extension includes multiple causes of delay, each cause should be listed separately, along with the amount of time granted for each, excluding any overlap. Time adjustments are sometimes granted for reasons unrelated to an excusable delay. Time adjustments are sometimes granted as part of a negotiated settlement and may not directly correlate with the progress schedule. Regardless of the reason for the extension, a revised Progress Schedule should be requested following execution of the change order. An example Time Adjustment Change Order is available.
The following statement is recommended for inclusion in all time adjustment change orders to make clear that the additional time being granted includes all excusable delays up to the date of the change order:
- “This revised Completion Date (or, “This addition of Calendar Days”), as specified, is full and final adjustment for all time and costs, loss or damage including, without limitation, delays, accelerations, or inefficiencies, resulting from the above causes, and is made without prejudice to the Commission.”
109.12.3.1 Excusable Delays for Unusual Events
Per Sec 108.14.1, the engineer may grant an excusable delay for unusual or extreme events. To qualify, the events must be highly unusual and not just somewhat out of the ordinary. For example, a wet construction season due to above average rainfall does not necessarily constitute “unusually severe weather”. In addition, the event must be outside of the contractor’s control and must have adversely affected the project's identified critical path schedule. Completed work damaged or destroyed by motorist or other outside parties may qualify as an excusable delay only if the remediated work adversely affects the project's critical path. When significant defects or failures in the contractor’s workmanship are discovered during the project and the remediation is extensive and results in significant time delays to the project's critical path, the State Construction and Materials Engineer may, at the State Construction and Materials Engineer's discretion, grant the contractor additional time to perform the remediation as part of a settlement agreement. The contractor shall submit in writing to the State Construction and Materials Engineer a justification request for the additional time. The justification must include the duration and timeframes to complete the remediation. In addition, an action plan that outlines the specific remediation shall be included with the justification. Only the time to perform remediation repairs will be considered for the additional time requests. The decision to grant additional time for these events are the sole discretion of the State Construction and Materials Engineer.
109.12.3.2 Description, Reason and Supporting Documentation
The Description/Reason narrative of the time adjustment change order, as well as the Supporting Documentation, should address four primary areas:
- 1. Describe the Contract Change - Begin by explicitly describing the change in contract terms. For example: “The number of Calendar Days for J4P2168, as stated in Section 2.1 of JSP B. CONTRACT LIQUIDAGED DAMAGES, is hereby increased from 130 days to 134 days.” Or, if the contract completion date is being extended, state: “The Contract Completion Date stated in Section 2.0 of JSP B. CONTRACT LIQUIDAGED DAMAGES, is hereby extended from Nov. 1, 2021 to Nov. 5, 2021.” If extensive changes are being made to the JSP, rewrite the JSP as desired, then merge it with the change order and state the following: “Delete JSP B. CONTRACT LIQUIDAGED DAMAGES and substitute with the attached version.”
- 2. Justification - Now explain the justification for the extension. For example: “The major operation, storm sewer pipe installation, was halted from March 15 thru March 18, both dates inclusive, to allow for the relocation of an unexpected water main owned by the City of Lee’s Summit, right of Sta 156+22. Per Sec 105.7.6.1, this delay is considered excusable but non-compensable.” If there are many details, provide those in the Supporting Documentation rather than the change order itself.
- 3. Full and Final Closure Statement - Insert our standard closure statement so that it is clear that this agreement is full and final. No additional cost adjustments will be made except for any terms that may have been included in the opening contract change statement. Insert the closure statement (cut/paste) exactly as it is written in EPG 109.12.3 Time Adjustment Change Orders. Just edit the part in parenthesis to match what type of time change you made (i.e., calendar days or date).
- 4. Supporting Documentation - Now provide Supporting Documentation, if necessary. This is an internal document to help reviewers and auditors understand the details. In the simple example above, everything was addressed in the change order itself, so no supporting documents would be needed. But, for example, had a weighted time table calculation been necessary, it would be shown in the Supporting Documentation. Or, perhaps a brief analysis of the critical path schedule is necessary to explain how the number of days granted was derived.
109.13 Prompt Payment to Subcontractors and Suppliers (for Sec 109.13)
Prompt payment of subcontractors is defined by Sec 109.13. The prime contractor shall coordinate with subcontractors to assure all subcontractors are paid within 15 days.
The Resident Engineer should provide the following to facilitate the process: The RE will provide an approved payment estimate to the prime contractor within 3 business days of the end of each estimate period. This approved payment estimate will provide a summary of all quantities paid to the contractor in order to facilitate the payment to the subcontractors.
Issues related to this subject can be forwarded to Construction and Materials. A related subject, Prompt Payment of Contractors, is related to RSMo Missouri Revised Statute 34.057.
109.14 Price Adjustment for Fuel (for Sec 109.14)
Prior to bid, the contractor must determine whether they will bid their project based on projected fuel prices, or if they will choose to utilize the fuel price adjustments provided in Sec 109.14. In their bid proposal, they will choose to accept or decline receiving a fuel adjustment for the bid items identified in Sec 109.14 when the contract is executed. Bidders must choose to accept or decline the fuel adjustments for qualifying pay items in each of the four categories: excavation (production), asphalt paving (production & hauling), concrete paving (production & hauling), aggregate base (hauling). Production factors account for fuel used in producing and placing a product (e.g. asphalt plant burner fuel, paver fuel, distributor fuel, etc.), whereas On-Road Hauling factors account for fuel used to haul the material to the project. The On-Road Hauling factor is based on a 30-mile round trip. This is an average factor that is always used regardless of the actual haul distance.
AWP automatically calculates the fuel price adjustment for all known qualifying standard pay items. Per Sec 109.14, non-standard pay items (generally designated with a "99" item number) do not qualify for fuel adjustment unless there is a Job Special Provision that overrides the spec and states the fuel adjustment shall apply to that item. Each estimate should be checked to verify that the appropriate fuel adjustments are being made either manually or auto-generated.
A Fuel Adjustment Calculation spreadsheet is available for manual calculations. Prior to calculating the adjustment, a check must be done to verify that the unit pay item matches the unit shown in the table in Sec 109.14. If not, a quantity conversion must be done before calculating the adjustment. For example, asphalt paid by the square yard would need to be converted to tons before multiplying by the corresponding factors in the table. The manually calculated fuel adjustment should then be added to the estimate as a CO Item Adjustments for the designated lines. The spreadsheet calculations should be retained in eProjects as documentation.
Payment for work should be made in the pay period (or at least a pay period in the same month) in which the work was performed in order for AWP to calculate the fuel adjustment accurately. If payment for work is submitted via AWP in a time period other than the month in which the work was performed, a manual fuel adjustment will be necessary. When this happens, the fuel price adjustment must be calculated for the correct estimate period and a contract adjustment must be made to correct for the difference in the index for the two estimate periods. Calculations should be retained with the contract documentation.
A table listing the Monthly Fuel Indexes is available in the right column under "Documents" on MoDOT’s Contractor Resources website.
The following table provides further guidance on when the fuel adjustment is applicable:
Pay Item | Does Fuel Adjustment Apply? |
---|---|
Asphalt pavement, shoulders, and entrances (full depth and overlays) | Yes, all asphalt in Sections 401, 402, 403 and ultrathin bonded asphalt wearing surface. |
Job Order contracts | Fixed-cost pay items in Job Order Contracts do not qualify because they are considered “repair” work and not “construction” work. This exclusion is stated in Sec 109.14. |
Concrete pavement (including pavement overlays), concrete base, shoulders, and entrances (i.e. 7” or 8” Paved Approach) | Yes. For overlays that have separate pay items for placing (SY) and furnishing (CY), only the square yards of placing should receive a fuel adjustment. For overlays that are paid entirely in CY, the unit of measure should be converted to SY and the adjustment should be paid based on SY at the theoretical thickness. |
Concrete Bridge Approach Slab and Concrete Approach Pavement | No |
Roller compacted concrete | Yes |
Concrete sidewalk, median strip (concrete or asphalt), or curb & gutter | No |
Full or partial depth pavement repair, asphalt and concrete | No, this concrete or asphalt material is for “repair”, not “construction”. Nor would the base rock for pavement repair. |
Concrete or asphalt bridge deck overlays | Deck overlays do not qualify except when the roadway asphalt overlay extends across the bridge deck. |
Seal coat, micro-surfacing, etc. | No |
Stabilized Permeable Base | Yes |
Type A2 and A3 shoulders (concrete and asphalt) | Yes, both the surface material and the base rock qualify, but not the portion of base rock identified as incidental. |
Aggregate surfacing | No, aggregate under Section 310 does not qualify. |
Other base rock such as 12" or 18" Rock Base (Section 303) | No. Only Type 1, 5, 7, and Stabilized Permeable Base qualify. |
Base produced from rock on the project or from an adjacent source | No, the material must be hauled to the project. |
Non-standard bid items. These are items not specifically listed in the Listing of Bid Items For Highway Construction at the time of letting (i.e. item numbers with a “99” designation). | No, not unless there is a JSP that specifically overrides Sec 109.14 and allows a fuel adjustment. |
109.15 Price Adjustment for Asphalt Cement
See EPG 403 Asphaltic Concrete Pavement for guidance on AC price index adjustments.