750.6 Erosion Control and Energy Dissipation: Difference between revisions
m →750.6.2.1 Shear Stress: Per Bridge, minor clarifications |
m →750.6.3.3 Rock Ditch Liner: minor correction |
||
Line 77: | Line 77: | ||
:<math>\tau_p\,</math> = permissible shear stress for rock lining, lb/ft<sup>2</sup> | :<math>\tau_p\,</math> = permissible shear stress for rock lining, lb/ft<sup>2</sup> | ||
:F = Shield's parameter, dimensionless = specific weight of stone, lb/ft<sup>3</sup> (typically 165 lb/ft<sup>3</sup>) | :F = Shield's parameter, dimensionless | ||
:'' | :''γ<sub>s</sub>'' = specific weight of stone, lb/ft<sup>3</sup> (typically 165 lb/ft<sup>3</sup>) | ||
:''γ'' = specific weight of water, 62.4 lb/ft<sup>3</sup> | |||
:d<sub>50</sub> = mean diameter stone size, ft | :d<sub>50</sub> = mean diameter stone size, ft | ||
Revision as of 07:39, 29 July 2014
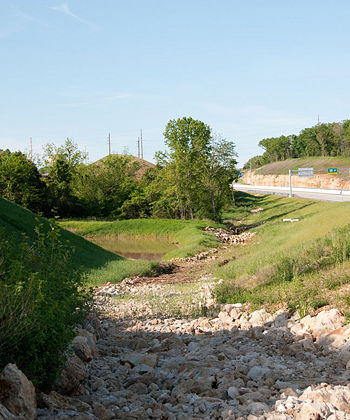
750.6.1 General
Providing for the control of erosion is a necessary part of the complete design of any highway construction project. These provisions must include measures for the control of both sheet and gully erosion during and after construction. This article is concerned with methods and criteria for the control of gully erosion in roadside channels and at culvert outlets. Control of sheet erosion is discussed in Embankment Protection and Pollution, Erosion and Sediment Control.
750.6.2 Erosion Control in Ditches
Control of ditch erosion is given careful consideration during design to reduce maintenance costs and to improve appearance. All ditches are analyzed to determine erosion control measures necessary to minimize maintenance. Ditch erosion is controlled by widening ditches, flattening ditch grades, or by application of proper ditch protection such as mulch, sodding, erosion control blanket, rock ditch liner and paved ditches. Economy is the prime factor for the final selection of the type of ditch protection. It is usually cheaper to widen ditches or flatten special ditch grades than to use sod, erosion control blankets, rock or pavement.
The selection of proper erosion protection consists of estimating the design flow rate at points along the channel length and determining the depth of flow and corresponding shear stress at these points, for various types of linings. The type of lining which will provide the necessary protection at the least cost is generally selected. The design flow rates at various points along the channel are computed by means of the rational formula as discussed in Hydrologic Analysis. The depth of flow in the channel is determined by means of open channel flow computations as discussed in Open Channels. The shear stress is determined by the method given below.
Ditches are designed to at least the minimum freeboard shown in EPG 748.3 Freeboard. Runoff and corresponding ditch flow depths and shear stresses are computed at random points as necessary to determine the limits of the various types of ditch protection required. After these limits have been determined, the design of all ditches is reviewed toward eliminating or minimizing required ditch protection by widening ditches or flattening ditch grades. Permanent conditions are analyzed in order to determine if a grassed waterway is adequate. If a grassed waterway is not adequate, then a rock ditch liner, erosion control blanket or paved ditch is specified and the design is complete. In medians it is sometimes more economical to provide for additional median drains to reduce velocity than to use ditch protection to prevent erosion. When ditches are located within the clear zone of a roadway, care must be taken to ensure the type of erosion control selected for the ditch does not negatively impact the traversability of the clear zone. Specifically, the erosion control should not snag, roll or otherwise prohibit an errant vehicle from regaining control within the clear zone. If rock ditch liner is used in the clear zone, only Type 1 is permissible. Ditches are designed without abrupt bends, where practicable. If abrupt bends are necessary, they are analyzed to avoid the possibility of overflow due to superelevation of flow and to determine the increased shear stress caused by the bend.
After the design flow rate has been computed and the channel slope has been established, the ditch section (usually a standard section) is analyzed as a grassed channel. This analysis is carried out by procedures outlined in Design of Channels with Flexible Linings. The permissible shear stress for various lining types is given in the Permissible Shear Stresses for Ditch Protection table. If the analysis shows that the permissible shear stress for a grassed channel is exceeded, then one of two things may be done. First, the ditch may be modified by widening the ditch section or flattening the ditch slope, if these actions are feasible. Second, the ditch may be lined with rock ditch liner or an appropriate erosion control blanket or the ditch may be paved. It should be noted that if the ditch is lined or paved, consideration should be given to reducing the channel dimensions. If the channel dimensions are reduced, a lined transition section should be used. The rate of channel width reduction should be on the order of 1 ft. of channel width for each 3 ft. of channel length. That is, each side of the channel should converge at a rate of 1 ft. in each 6 lineal feet.
750.6.2.1 Shear Stress
The forces created by flowing water in a channel exert a shear stress on the channel boundaries. The maximum stress for a straight channel occurs on the channel bed and is less than or equal to the shear stress at maximum depth. The maximum shear stress is given by:
- where:
- = maximum shear stress, lb/ft2
- = unit weight of water, 62.4 lb/ft3
- d = maximum depth of flow, ft
- S = average bed slope or energy slope, ft/ft
Flow around a channel bend imposes higher shear stresses on the channel boundaries. The maximum shear stress in a bend is a function of the radius of curvature and the bottom width of the channel and is given by
- where:
- = maximum shear stress in a bend, lb/ft2
- Kb = bend coefficient - function of Rc/T
The bend coefficient is given by
Kb = 2.00 Rc/T<2 Kb = 2.38 - 0.209 (Rc/T) + 0.0073 (Rc/T)2 2<Rc/T<10 Kb = 1.05 Rc/T>10
- where:
- Kb = bend coefficient - function of Rc/T
- Rc = radius to centerline of channel, ft
- T = top width of channel, ft
The increased shear stress due to the bend persists downstream of the bend a distance Lp, given by
- where:
- Lp = length of protection downstream of the point of tangency, ft
- n = Manning’s roughness coefficient in the bend
- R = hydraulic radius, ft
750.6.3 Types of Ditch Protection
There are several types of ditch protection available, as described in the following paragraphs, the Permissible Shear Stresses for Ditch Protection table and in the Storm Water Pollution Prevention Plan (SWPPP).
750.6.3.1 Mulch
Mulch is the default type of ditch protection and is to be used in all ditches where sod, rock ditch liner, erosion control blankets or paving are not used. Mulch is a temporary treatment, and is used to prevent erosion of the ditch until permanent vegetation is established. Properties of the soil and anticipated permanent vegetation are used to calculate flow depth and shear stress when mulch is used. For initial design, approximate permissible shear stress values are provided in the Typical Permissible Shear Stresses for Ditch Protection table.
750.6.3.2 Sod
Sod may be used as a ditch liner within its permissible shear stress. Properties of the soil and anticipated permanent vegetation are used to calculate flow depth and shear stress when sod is used. For initial design, approximate permissible shear stress values are provided in the Typical Permissible Shear Stresses for Ditch Protection table. Sod is provided to at least a 3 in. above the depth of flow in the ditch.
750.6.3.3 Rock Ditch Liner
Rock ditch liner consists of a predominantly one sized, durable stone, shot rock or broken concrete placed by dumping and left in a rough condition to the approximate shape of the specified ditch. Rock ditch liners are designed to at least the minimum freeboard shown in EPG 748.3 Freeboard. All computations are based upon the nominal ditch shape. Details for rock ditch liners are shown in the standard plans. Manning's roughness coefficient, "n", varies according to flow depth and mean diameter stone size (d50) required, as discussed in Uniform Flow Calculations. Permissible shear stress for a rock lining is also a function of the mean diameter stone size. Permissible shear stress is given by
- where:
- = permissible shear stress for rock lining, lb/ft2
- F = Shield's parameter, dimensionless
- γs = specific weight of stone, lb/ft3 (typically 165 lb/ft3)
- γ = specific weight of water, 62.4 lb/ft3
- d50 = mean diameter stone size, ft
Setting the permissible shear stress equation equal to the shear stress equation given in EPG 750.6.2.1 Shear Stress multiplied by a safety factor the following sizing equation for d50 can be derived.
The Shield’s parameter can vary and is linked to the particle Reynolds number. The particle Reynolds number is given by:
- where:
- Re = particle Reynolds number, dimensionless
- V = shear velocity, ft/s
- ' = kinetic viscosity, 1.217 x 10-5 ft2/s at 60° F
Shear velocity is defined as:
- V =
- where:
- g = gravitational acceleration, 32.2 ft/s2
- d = maximum channel depth, ft
- S = channel slope, ft/ft
Selection of Shield’s Parameter and Safety Factor | ||
---|---|---|
Reynolds Number | F | SF |
< 4 x 104 | 0.047 | 1.0 |
4 x 104< Re < 2 x 105 | linear interpolation | linear interpolation |
> 2 x 105 | 0.15 | 1.5 |
The lowest practical type of rock ditch liner should be selected based on permissible shear stress calculations. For constructability, short intervals of different types of rock ditch liner should be avoided. When economical, the larger size type of rock ditch liner should be extended to eliminate short segments of a smaller type rock. Type 1 and 2 are very similar in cost, so it is desired to extend Type 2 through a short segment where Type 1 is calculated to be acceptable. Similarly, Type 4 should be extended through short Type 3 segments if both are required. This is not the case for Type 2 and 3, because Type 3 requires a bedding layer and Type 2 doesn't, making the cost for Type 3 significantly higher than Type 2. Geotextile filter fabric should be used under all rock ditch liners except where grades are less than four percent and the District Soils and Geology Technologist determines that the geotextile is not necessary. Generally, geotextile fabrics are not required for clays or silty clays with a liquid limit greater than 30. Aggregate bedding material is required under all Type 3 and Type 4 rock ditch liner. Details for rock ditch liners, geotextile fabrics and bedding materials are shown in the standard plans.
750.6.3.4 Erosion Control Blankets and Turf Reinforcement Mats
Five types of erosion control blankets are available for temporary use. Turf reinforcement mats can be used to supplement permanent erosion control. Refer to EPG 806.8.4.3.10 Erosion Stabilization Mats and Blankets.
750.6.3.5 Gabion Lining
Gabions (rock filled wire containers) represent an approach for using smaller rock size than would be required by riprap. The smaller rock is enclosed in larger wire units in the form of mattresses or baskets. Gabion baskets are individual rectangular wire mesh containers filled with rock and frequently applied for grade control structures and retaining walls. Gabion mattresses are also rock filled wire mesh containers. The mattresses are composed of a series of integrated cells that hold the rock allowing for a greater spatial extent in each unit. Potential roadside applications for the gabion mattress include steep channels and rundowns. Permissible shear stress is estimated based on the size of rock fill or the gabion mattress thickness. Both estimates are determined and the largest value is used as the permissible shear stress. Gabion liners are designed to at least the minimum freeboard shown in EPG 748.3 Freeboard.
Permissible shear stress based on rock fill size is given by:
- , for 0.25’ < d50 <1.5’
- where:
- F = Shield’s parameter, dimensionless (0.10 for gabions)
- = specific weight of stone, lb/ft3 (typically 165 lb/ft3)
- = specific weight of water, 62.4 lb/ft3
- d50 = mean diameter stone size, ft
Permissible shear stress based on mattress thickness is given by:
- , for 0.5’ < MT < 1.5’
- where:
- MT = gabion mattress thickness, ft
- MTc = thickness constant, 4.07 ft
750.6.3.6 Typical Permissible Shear Stresses for Ditch Protection
Lining Category | Type | Permissible Unit Shear Stress | |
---|---|---|---|
lb/ft2 | |||
Permanent | Vegetation Class A | ||
Vegetation Class B | |||
Vegetation Class C | |||
Vegetation Class D | |||
Vegetation Class E | |||
For description and selection of vegetation class see Open Channels - Manning's n | |||
Rock Ditch Liner Type 1 | |||
Rock Ditch Liner Type 2 | |||
Rock Ditch Liner Type 3 | |||
Rock Ditch Liner Type 4 | |||
Turf Reinforcement Mats | See EPG 806.8.4.3.10 | ||
Gabion Lining | Varies See EPG 750.6.3.5 | ||
Temporary | Erosion Control Blankets | < 3.5 See EPG 806.8.4.3.10 | |
* Values are approximate, actual design values should be calculated. |
750.6.3.7 Paved Ditch
Paved ditch consists of a concrete lining which is formed and finished. Paved ditch is only used in urban areas where aesthetics are of importance. These ditches are designed to at least the minimum freeboard shown in EPG 748.3 Freeboard. Construction details may be found in the standard plans. Manning's roughness coefficient "n" of 0.015 is recommended.
The use of sod, geotextile fabric or erosion control blanket should be considered along the top edge of the paved ditch, as required by soil conditions, to eliminate potential for undercutting of the paved ditch.
750.6.4 Interception Levees and Ditches
Interception levees and ditches are provided at the top of earth backslopes at all locations where the natural ground slopes toward the backslope. Where the natural ground is on a slope that will allow the area back of the levee to drain, levees only are provided. In such cases, the natural sod will provide erosion protection. Levees and ditches are provided where the area back of the levee will not drain without ditches. Interception ditches receive the same erosion control analysis and treatment as other ditches using the same controls, with particular attention being given to the outlets. Typical details for interception levees and ditches are shown in the standard plans. Interception ditches and levees are shown on the plan profile sheets by proper legend and are tabulated on the 2B sheet by listing station limits, side, estimated lengths, and ditch width where necessary. Interception ditches and levees are not shown on cross section sheets.
750.6.5 Erosion Control at Culvert Outlets - General Criteria

Since culverts are hydraulically efficient, the velocity of flow through a culvert is greater than the velocity of flow in a natural channel of the same slope. When this high velocity flow exits the culvert, a scour problem may develop. Scour holes at culvert outlets develop because of the need to dissipate excess energy. These scour holes may undermine the culvert headwall and endanger the structure or damage the embankment. Therefore, the potential for scour at all culvert outlets should be investigated.
In general, an existing streambed which is old and well-seasoned will withstand much higher velocities than will a channel which has been newly constructed. This is because erosion has been taking place in the natural channel for many years and the material forming the channel lining tends to be coarse and stable. Therefore, allowable outlet velocities at culvert outlets, which discharge into a natural stream, tend to be higher than the velocities allowed in new roadside channels.
The Stability of Natural Channels at Culvert Outlet is presented as a guide to aid the designer in determining when scour protection is needed at culvert outlets. In this figure, the stability of the channel at the culvert outlet is shown as a function of the culvert outlet velocity and the mean stone size of the channel bed. This figure is based on cohesionless soil conditions and is therefore conservative when a gravelly streambed with a clay binder is encountered. When such a cohesive binder is present, the maximum velocity for a given mean stone diameter may be increased by 2 to 3 ft/s. Occasionally a streambed is located on bedrock. In this case, the figure does not apply and no special erosion control measures are necessary.
If it is determined that culvert outlet protection is needed and the calculated outlet velocity is 20 ft/s or less, then a rock lining should be provided. For outlet velocities greater than 20 ft/s, an energy dissipator such as internal baffle rings, an impact type energy-dissipating headwall or a culvert outlet flume will be required. The type of energy dissipator chosen depends on site characteristics. Internal energy dissipators should be used only in situations where debris is not considered a problem. Rip-rap lined stilling basins (pre-formed scour holes) can be used where the expected scour hole is acceptable and there is no nuisance effect. Impact-type dissipators and stilling basins are used where the scour hole is not acceptable and/or debris is present. Impact-type dissipators are effective when outlet velocities are moderate and the Froude number is less than 3.0. Stilling basins can be used for higher velocities and Froude numbers greater than 3.0. Additional information on design of energy dissipators can be found in the FHWA HEC-14 publication Design of Energy Dissipators for Culverts and Channels.
Use of “broken-back” culverts is generally not recommended as a method of reducing outlet velocities. The broken-back design is based on the assumption that the reduced slope of the lower portion of the barrel will operate under subcritical conditions, thereby lowering velocities; however, tailwater depths are rarely sufficient to force a hydraulic jump inside the culvert barrel and very little reduction in outlet velocities is achieved under those circumstances. If a broken-back culvert is used to reduce outlet velocities, open channel flow calculations must be performed to verify that the intended result is achieved.
750.6.6 Rock Lining at Culvert Outlets
Rock lining is used for scour protection at culvert outlets when it is determined that the natural streambed will not withstand scour and the culvert outlet velocity is 20 ft/s or less. The rock lining is rectangular in shape and consists of dumped rock blanket material placed in an excavation at the culvert outlet. This material is to be paid for as Rock Lining. Since the material is dumped and not hand placed, no payment will be made for placing rock lining. This treatment is not used where rock is existing in the channel.
The minimum dimensions of the rock lining are a function of the culvert size and are given in Standard Plan 609.70. The culvert size in this table is given as the diameter of a circular pipe. However, the dimensions shown can be applied to box or arch culverts of equivalent waterway area.
The mean velocity at the downstream end of the rock lining may be calculated by the Manning Formula applied to the channel cross-section through the rock lining.
750.6.7 Impact Type Energy Dissipator
Impact type energy dissipators are based on designs developed by the US Bureau of Reclamation (USBR) and are equivalent to the USBR Type VI basin. They may be used at culvert outlets requiring scour protection where the outlet velocity is greater than 20 ft/s. These energy dissipators will give adequate hydraulic performance when operating at velocities up to 33 ft/s and discharges up to 400 cfs. Scour protection from outlet velocities greater than 33 ft/s or discharges greater than 400 cfs cannot be provided by a standard design. If outlet velocities greater than 33 ft/s or discharges greater than 400 cfs are encountered in design, consideration should be given to modifying the design to reduce outlet velocity. For example, reducing the slope of the structure by employing a drop inlet type entrance may result in an outlet velocity reduction.
Details of the energy dissipating headwalls are shown in Standard Plans 604.10 to 604.15:
- Standard Plan 604.10
- Standard Plan 604.11
- Standard Plan 604.12
- Standard Plan 604.13
- Standard Plan 604.14
- Standard Plan 604.15
Unlike stilling basins which utilize a hydraulic jump for energy dissipation, the impact type energy dissipator requires no tailwater for successful performance. In addition, a properly designed impact type energy dissipator will outperform a hydraulic jump as an energy dissipation device. Energy dissipation is achieved by virtue of the vertical hanging baffle. When the high velocity flow exits the culvert, it strikes the baffle and is turned upstream in vertical eddies, thus reducing the energy and velocity of flow.
It is important that the impact type energy dissipators shown in the standard plans be utilized only for outlet velocities of from 20 to 33 ft/s. If these dissipators are overdesigned, that is, used on culverts with maximum outlet velocities less than 20 ft/s, then the incoming jet of water will pass under the baffle and effective energy dissipation will not occur. If these dissipators are under-designed, that is, used on culverts with maximum outlet velocities greater than 33 ft/s, then the water will overflow the baffle. This overtopping may cause erosion around the sides and along the toe of the energy dissipator as well as reduce the hydraulic efficiency of the structure.
Hydraulic Performance of an Energy Dissipating Headwall graphically illustrates the hydraulic performance of an impact type energy dissipator. This figure shows the energy and velocity loss induced by the energy dissipator as a function of the culvert outlet energy, velocity and Froude Number. In this figure, "E" is the energy of flow into the stilling basin, "EL" is the energy loss induced by the stilling basin, "V" is the velocity of flow into the stilling basin (culvert outlet velocity) and, "V2" is the velocity of flow out of the stilling basin. This figure is valid if the stilling basin is operating at or near its design capacity.
The Froude Number used in the evaluation of the hydraulic performance of an impact type energy dissipator is mathematically identical to the Froude Number as defined in Uniform Flow Calculations. However, the hydraulic depth, "D" is defined differently. As used here, the hydraulic depth is defined as the square root of the culvert waterway area; i.e. D = (A)1/2, expressed in feet. Although the energy dissipating headwalls shown in the standard plans are proportioned based on circular culverts, they may be used on arch and rectangular shaped culverts of equivalent waterway area.
The toe of the energy dissipating headwall may be provided with a small section of rock lining. This rock lining is square in shape with the width and length both equal to the width of the headwall. If the natural streambed contains rock of a mean stone size equal to or greater than that given by Hydraulic Performance of an Energy Dissipating Headwall, the rock lining is not necessary. If the rock lining is found to be necessary, then dumped Type II Rock Blanket material 2 ft. thick should be specified.
750.6.8 Culvert Outlet Flumes
The St. Anthony Falls (SAF) stilling basin, employing a flume and stilling basin, has been used with success. This device utilizes a hydraulic jump to dissipate excess flow energy. Roughness elements on the stilling basin floor and an end sill are used to form and control the jump. The USBR Type IV stilling basin is similar, but may be smaller in size and thereby lower in cost. In general, a stilling basin should only be used in areas of very erosive soils such as loess, or on structures larger than those for which standard energy dissipating headwalls are available. Design procedures and other details for both types of stilling basins can be found in Section VII of HEC-14.
750.6.9 Internal Baffle Ring Energy Dissipators
A system of internal baffle rings may be used to increase resistance and reduce velocities at the outlet of pipe culverts flowing partially full in inlet control. A series of five rings are employed at the downstream end of the culvert, with specific spacing and ring height requirements. The baffle rings should not be used when significant amounts of debris can be expected. Design procedures for the internal baffle ring dissipators can be found in section VII-C of HEC-14. Since ring height and spacing vary from application to application, a Special Sheet, which can be modified for a particular application, is available from Design's Engineering Policy Group.