902.19 Construction Inspection Guidelines for Sec 902

General (Sec 902.2)
Installation of traffic signals can be considered, for the most part, as erecting, installing, and wiring of specialized equipment to control flow of vehicular and pedestrian traffic. Types of control equipment currently specified vary greatly in their makeup and in necessary associated equipment. The type of control equipment specified for a particular project is based on geometrics of the intersection, anticipated volume of traffic that will use the facility, and proximity of other intersections.
Regardless of the type of control equipment specified or geometrics of the intersection involved, construction procedure is approximately the same for all signal projects. The order of work consists of: (a) laying or pushing conduit network; (b) excavating, forming, and placing of pullboxes, post bases, and controller bases; (c) erection of signal posts; (d) installation of electrical service; (e) installing signal heads; (f) installing detectors; (g) pulling cable into conduits; (h) tagging and wiring signal heads, detectors, interconnection system, and controller; (i) checkout of individual components and final checkout of the entire system. It is the intent of this article to set out inspection procedures in the same general order as work is usually done.
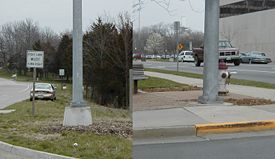
The inspector assigned to a signal project should thoroughly study the contract. If the inspector has had no previous signal work, they can gain much by study of a previously completed installation. Discussions with Traffic are very helpful. They can explain the various types of equipment to be used and give the inspector a better understanding of nomenclature used in signal work.
The list of equipment and material that the contractor submits for approval serves the same general purpose as does the list for highway lighting. See Sec 901.2.
In the event that some questions arise about manufacturer's terminology, the district traffic personnel will be able to clarify any questions. Terminology will vary slightly from manufacturer to manufacturer but the general concept remains the same.
Staking
Staking and layout work for a traffic signal project should be done with the idea always in mind to avoid conflicts with roadway items, and with signing and lighting if they are included in the project. Each signal post location shall be staked and carefully checked to see that signal heads to be mounted thereon will be in clear view from the lane, or lanes, to be controlled. Posts should not be located in sidewalks if it can be avoided without reducing visibility of signal heads. Pullbox, conduit runs, and controller base locations may have to be shifted to avoid conflict with other items. Care should be taken to avoid placing signal appurtances in a drainage ditch. If necessary, shift the controller base to a location where chances of its being struck by a vehicle are reduced to a minimum. If the controller base is so situated that it cannot be moved it may be necessary to place a section or more of guardrail around the controller to provide adequate protection.
Glossary
In the event that some questions arise, the district traffic personnel will be able to clarify any questions. Terminology will vary slightly from manufacturer to manufacturer but the general concept remains the same.
Installation of Posts and Signal Heads (for Sec 902.5)
Before erection of posts and hanging of signal heads, the inspector is to check equipment for shipment damage. The inspector is to also check the numbers of the various items to see that they agree with the numbers on the previously approved list. Inspect posts for plan dimension and signal faces for plan diameter and the arrow and pedestrian lens for compliance with standard drawings. Check for correct clearances of Types C, CL, BL and B signal posts from overhead power lines.
Signal posts with Type S and Type T signal heads are erected in a vertical position by adjustment of leveling nuts. Signal heads as well as arrow signal lenses are to be installed in final position with vertical edges plumb as checked with a spirit level. An otherwise satisfactory installation can give an unsightly appearance if signal heads are canted from plumb or arrow lenses point in a slightly different direction from plan.
Signal arms shall be raked upward at 0.25 in. per ft. minimum.
Signal heads on mast arms shall be tilted forward from the top 3 to 7 degrees.
After signal heads have been wired and power is supplied to the controller cabinet, signal faces should be aimed. All signal indications should be verified by applying momentary power to each field wire termination at this time. An optically programmable signal head is sometimes used when it is necessary to limit the visibility zone to specific lanes and areas. Manufacturer’s instructions for installation will provide enough data for an inspector to check this type of signal head properly.
The current specifications only allow the contractor to utilize signal housings made of polycarbonate material. Polycarbonate housings are less costly and lighter in weight. The inspector is to check all connections, both electrical and mechanical, to ensure all are tightened securely.
Power Supply Assembly (for Sec 902.9)
Refer to Sec 901.
Service Pole Installation (for Sec 902.9.1)
This item of work is usually done while underground conduit is being installed. Location and arrangement of equipment on the service pole is to be cleared with the supplying utility. Conductor cable that supplies power to the controller is to be tested for shorts and grounds after installation. This procedure is to also check incoming secondary voltage for design tolerance of plus or minus 5 percent voltage drop. Generally, 120-volt service is supplied to the controller cabinet.
Traffic Controller Assemblies (for Sec 902.11)
Types Of Controllers
- Solid State Fixed Or Pre-timed Controllers. In some instances, a pre-timed controller is used as a semi-actuated controller. This is accomplished by installing loop detectors in a left turn lane or a side street approach. A vehicle entering the zone of influence of the loop will cause the pre-timed controller to display a 3- or 4-second yellow to the phase having the green light and then the side street or the left turn traffic is allowed green time to clear the intersection. Depending upon whether the intersection is operating in an isolated manner or is interconnected to a system, the side street or left turn green will be given fairly soon depending upon the status of the controller.
- The accuracy of time settings on solid state controllers is very high since their time base is established from the 60 hertz incoming power frequency. All models have a battery back up so that the timing memory and other programs are not lost in the event of AC power failure.
- Solid state pre-timed controllers use the keyboard entry method of establishing timing functions. A display enables the inspector to see the amount of time allotted for each particular function. These controllers also have interconnection features allowing them to be monitored in a system by a solid state or electromechanical master controller. In order to prevent unauthorized people from changing any timing on this type of equipment, access to the keyboard is denied until a coded sequence of access numbers are first entered in the keyboard.
- Solid state, pre-timed controllers use solid state load switches to control the intersection signal lamps. A fail-safe monitor is also required to prevent conflicting indications from being displayed and detect other failures.
- Pre-timed Solid State Master Controllers. This type is a special controller generally used to supervise one or more electromechanical pre-timed controllers, solid state pre-timed controllers and actuated solid state controllers. When specified, this controller may: effect a transfer from one timing plan to another at local controllers; establish time offsets between local controllers so that traffic may progress through a series of intersections with minimum delay; provide for railroad, fire, or emergency vehicle pre-emption; provide a regularly scheduled program for local controllers to follow on a week to week basis; and other features.
- The inspector should ask the contractor to demonstrate each of the master controllers’ specified functions. If local controllers are in operation and traffic is using the intersections, the master controller checkout is to be made during off-peak traffic periods.
- Pre-timed, Solid State Master Controllers. This controller may supervise one or more electromechanical pre-timed controllers, solid state pre-timed controllers and many actuated or solid state controllers. Coordination between the master controller and local controller may be accomplished by multi-conductor cables, telephone voice grade wire pairs or by utilizing time based coordination.
- Solid State Actuated Controllers. Timing for these controllers are entered by keyboard. All signal lamp load switches are also solid state. Our specifications require a fail-safe device known as a conflict monitor. This monitor is hardwired into the output side of each load switch and when a load switch failure occurs the signals are switched into flashing operation immediately.
- The inspector can determine by observing the controller display what interval is being timed, detector calls coming in, next phase waiting for the right of way and other information. Some controllers have a digital read-out showing a countdown of the time remaining in any particular interval. The monitor program card shall be checked prior to signal turn on for proper configuration. The inspector is to have the contractor check the operation of the conflict monitor by momentarily shorting two conflicting green indications together at the point where they are terminated in the bottom of the controller cabinet. A word of caution here - use an insulated jumper wire and try to select a period of light traffic in order to cause a minimum of inconvenience to motorists.
- All conflict monitors have indicating lights to show when they are in operation and they also have a reset button which reactivates the controller into normal operation. The inspector is to check traffic flow in the intersection before pushing the reset button because when the controller reverts from flashing it returns to normal signal operation.
Auxiliary Control Equipment
In addition to the previously mentioned controllers, there are several types of auxiliary control equipment which are specified to increase efficiency of the main control equipment, provide for railroad and emergency vehicle pre-emption and other special functions.
Preemption Equipment
At some locations there is a need to interrupt normal signal operation to provide special service to accommodate an approaching train or fire and other emergency vehicles. At these locations, special preemption equipment is installed to provide a means for activating a special signal sequence. The inspector should ensure that complete testing of preemption equipment is performed. Documentation of successful testing should be provided to the district Traffic department and to district signal shops.
Fire Station and Emergency Vehicle Preemption
Fire or emergency vehicle pre-emption can be initiated by a switch located in a nearby fire station or emergency facility or by a special emitter that can be mounted on emergency vehicles.
Manual switch
The manual switch is connected to the signal control cabinet by cabling or via a radio connection. Activating the switch will initiate a pre-empt sequence in the affected. Pre-emption timing, in this case, depends upon the time it will take for an emergency vehicle to leave its building and clear the controlled intersection. This is best determined from an actual test run by an emergency vehicle.
Emitter
For initiating fire or emergency vehicle preemption by means of a special emitter that can be mounted on emergency vehicles, receivers are mounted on the signal structures that will detect the presence an emitter-equipped emergency vehicle and provide the preemption input into the signal controller. Typically the signal controller’s response is to favor the direction that the emergency vehicle is traveling. Operation of this system is best tested by an actual test run of an emitter-equipped emergency vehicle.
All equipped approaches should be tested.
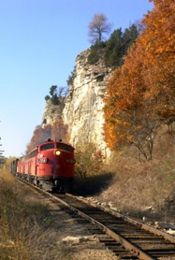
Railroad Pre-emption
In certain cases where a railroad crossing is near a signal installation, the pre-emption equipment is placed in operation when detectors installed on the tracks are actuated by an approaching train. The train detection and rail crossing equipment is typically owned and maintained by railroad personnel. A cable connects the railroad’s control equipment to the affected traffic signal controller. Cooperation with the railroad company is needed for checking these systems. A typical railroad preemption sequence begins with providing a green signal to the appropriate signal approaches in order to clear the tracks of any vehicles. After track clearance, the signal will operate in either a flashing mode or in a limited service mode where only those movements that do not cross the tracks are allowed. After the train has cleared the area the traffic signal returns to normal operation.
The inspector should check the signal sequence during the preemption cycle to see that yellow clearance intervals are displayed before signals turn red and that signals operate so as not to trap vehicles on the tracks.
Controller Installation
General. Regardless of type of control equipment specified for a particular project, certain procedures are common to all installations. Controller installation consists of the following separate operations:
- (1) Identification and tagging of all incoming cables
- (2) Placing controller housing on concrete base or wood pole
- (3) Stripping the jacket from each cable and identifying each conductor
- (4) Cutting, grouping, splicing and terminating of incoming conductors to controller terminal strip
- (5) Termination of incoming power supply
- (6) Checking of all detectors
- (7) Final checking of the entire system.
During these phases of work the inspector should check tagging of cables for specification compliance. All signal head cables should be terminated on a terminal strip located at the bottom of the control cabinet. Every terminal connection should be checked to see that conductors are held firmly in place. Conductors leaving the conduit should be bunched and laced up neatly before they are fanned out to terminal strips. It is the contractor’s responsibility to make proper terminal connections. The contractor is to check each conductor to determine if it is connected to the proper terminal before the system is placed in operation. The inspector should become familiar with the various circuit diagrams to gain a better understanding of the work involved. After the contractor has finished his conductor terminations the inspector shall require incoming conduit or conduits to be sealed in accordance with Sec 902.15.2.
The inspector should check that all housing vents are free of obstructions and properly screened. If a ventilating fan is specified, the inspector should ascertain that it operates when the cabinet temperature reaches approximately 90 degrees F.
Detector Installation (for Sec 902.13)
The purpose of any vehicle detector is to sense the passage or presence of a vehicle approaching an intersection and relay this information to the controller for processing. It is the purpose of this article to explain briefly the theory of each type of detector and proper installation techniques. Proper location of detectors is important and if there are any questions consult Traffic.
Induction Loop Detector (for Sec 902.13.2)
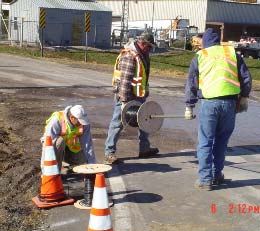
This type of detector consists of a loop of cable embedded within the roadway. When the loop is connected to the detector amplifier in the cabinet it completes a tuned circuit. When a vehicle enters the loop area, a resultant shift in the resonant frequency of this tuned circuit is detected and the detector amplifier places a call in the controller. The locations of traffic signal loop detectors and the locations of the stop bars at intersections are critical. Improper location of these two features in relation to each other can cause operational problems with the traffic signals. Ideally, the two features are located so that when a vehicle stops at the stop bar, the stopped vehicle is fully in the detection zone of the loop. Care also needs to be taken when side street left turns are present. Locating the stop bars too far forward in these situations can either make it difficult for the side street traffic to execute their left turn or the turning traffic could clip the loop, thereby putting a false detection into the signal.
When intersection markings using durable materials are to be installed at intersections with traffic signals, the installation sequence of the detector loops and permanent pavement marking is important. Coordination of the layout of stop bars and loops with traffic personnel is encouraged for proper placement of both. The detection loops should be cut and sealed first, followed by placement of the stop bars. This sequence is recommended so that the durable pavement marking tape is not cut or damaged by the saw cutting process for the detector loops. Preparation needed for installing the markings must not damage the loop detectors.
Installation of the loop detector begins with sawing a slot in the pavement. This saw cut is to be made by wet cutting. If the slot crosses an expansion joint, depth must be increased slightly to provide a little play in the cable for expansion. Placement of loop slots across cracks and joints should be avoided if at all possible. On resurfacing projects when new loops are to be installed be sure the old loop is destroyed by cutting through the loop wire to prevent it from providing false calls.
Before cable is placed in the slot, all debris and moisture must be removed. The cable is then placed in the slot and pushed into proper position by use of a blunt nonmetallic object.
The roadway loop cable is spliced to a twisted shielded two conductor cable in the nearest junction box or pullbox by means of a waterproof splice. Before the pavement slot is filled, a resistance test is required. A minimum 10 megohm resistance to ground reading at the controller cabinet is necessary. Following a satisfactory resistance test the sawed slot is filled with sealing compound. Ensure the loop does not float up while sealing. Methods for tuning and operation of the induction loop detector vary among manufacturers, therefore manufacturer’s operating instructions are to be followed.
The loop wire between the loop and the nearest pull box shall be twisted at least three turns per foot.
Pedestrian Push Button Detectors
This type detector is a manually operated switch mounted near a crosswalk entrance. It permits pedestrians to call for right of way at a signalized crosswalk. Installation of these detectors are covered on standard drawings and in specifications. The inspector should ensure that pushing the button places a call in the controller for the proper crosswalk phase. The inspector also ensures the proper symbols are displayed on the pedestrian signal heads in the appropriate sequence.
Other types of detector installation
For other types of detectors, including microwave and ultrasonic detectors (Sec 902.13.3) and video dectection systems (Sec 902.13.4), the inspector should follow the recommendations of the manufacturer.
Pull and Junction Boxes (for Sec 902.14)
The inspection of excavating, forming and placing concrete for pullboxes or aprons should be done in a manner similar to that set out in Secs 902.14 and 902.20. Early attention should be given to establishing the proper final grade for all pull boxes. The inspector must also make certain that conduit openings are properly installed in the sides of the pull box. Conduits turned up into the bottom of a pull box should not be allowed.
It is important to ensure that pull boxes drain properly. The standard drawing depicts two types of pull box drains. If a Type I drain is used, ensure that the proper depth of stone is used. If it becomes evident that, due to the nature of soil or due to the elevation, a particular pull box will not drain properly, it may become necessary to provide a conduit drain in lieu of the stone drain provided on plans. During finish work all cabling should be neatly tied to the cable hooks provided in the pull box.
Concrete Bases
The inspection of concrete bases should ensure that conduits are capped, and that ground rods and anchor bolts stay in proper position during concrete placement. Adequate vibration of the concrete is necessary to fill all voids. The contractor is required to protect anchor bolt threads during concrete placement. All concrete should be removed from any signal equipment including threads immediately after finishing has been completed.
Additional information regarding the inspection of post bases and controller bases can be found in Secs 902.15.1 and 902.15.2 and Standard Plan 902.30.
Conduit Systems (for Sec 902.16)
Conduit runs are generally graded a minimum of 0.5% for drainage. If a long conduit run will have a flat grade between two pull boxes, and it is not possible to lower the grade on either end, the conduit should be “humped” in the middle to drain in both directions. A typical case where it is very difficult to grade conduit runs properly is where a conduit has to be jacked or pushed beneath an existing roadway with a rocky sub-base.
All fittings and joints should be checked for tightness. Extra care should be taken at locations where a transition between rigid steel, polyvinyl chloride (PVC), or high density polyethylene (HDPE) conduits takes place. HDPE is impervious to chemicals and adhesives so sound mechanical joints must be ensured. Any empty conduits installed for future use should have a locatable tracer wire and a pull rope installed.
Refer to Sec 902.16 for information regarding conduit systems including metal conduit, polyvinyl chloride conduit, conduit in trench, pushed conduit, conduit in a median and conduit on a structure.
Installation Of Conductor Cable (for Sec 902.19)
Measuring, cutting to proper length, and pulling of conductor cable into conduits and handholes, even though a slow and laborious process, will be carefully inspected. Strict specification enforcement is necessary to prevent cable damage. Insulation resistance tests to detect shorts and grounds are not required except in installation of power cables; however, it is to the contractor’s advantage to make such tests with an ohmmeter or multimeter as they are checking for continuity and tagging circuits. Items are to be checked to see if they agree with the products list approved.
The inspector ensures the contractor uses red, orange and green color-coded wires for like colored signal faces on the main artery or street. This will help the contractor in circuit identification at the controller. It will also help in future maintenance work. The inspector also requires the white conductor in each cable to be a neutral or common return.
Test Period (for Sec 902.21)
Controller Checkout
Certain procedures should be followed in testing a controller before acceptance. If the installation is to be placed in operation under traffic, it is suggested that the local police force be asked to have at least one officer present during testing of a controller, unless otherwise provided in the contract. Lane markings and stop lines at the intersection shall be in place before placing signals in operation. Also, right before signals are powered for flashing operation certain regulatory signs (temporary stop signs) are to be removed.
Refer to Standard Specification section 902 for signal turn on procedures. There are definite procedures to be followed by the inspector to assure that the controller functions in accordance with the contract. Existing signals should not be removed until the new signals have proven to operate properly.
New signals require an adjustment period. There will often be signal violations during the first few days of operation. Initial controller timing might require adjustment for maximum efficiency. Traffic personnel should be consulted when timing changes are required.
Detector operation should be checked before turning on signal indications. Detector settings should be adjusted for proper coverage so vehicles passing through the detector will cause positive action at the controller.
When the inspector is sure the controller, detectors and auxiliary equipment are operating properly and timing is approximately correct, the inspector will have the contractor turn on the signal indications. It is best to watch for a gap in traffic volume to switch the signals on. The inspector checks all signal indications to see that they are displayed in sequence and are aimed properly to direct traffic. During this time the inspector watches traffic movements to see whether the controller is timing movements so there is minimum congestion.